4 Maintenance
4.1 Basic description
The maintenance of the machine should be carried out in such a way as to ensure that the machine is kept in a functional and productive state or that it is restarted for a short period of time in the event of a breakdown.
Being fully responsible for maintenance means that it is up to the machine owner to ensure the availability and increase the life of the machine.
All upkeep, inspection and maintenance must be repeated continuously at the specified intervals. The following categories shall be distinguished here:
- Upkeep
- To slow down wear and delay undesired machine stoppages, inspection and maintenance work should be performed.
- Inspection
- To determine and evaluate the actual condition of the machine, including recording wear and tear and performing the necessary maintenance.
- Upkeep and maintenance
- Ensure the function of the machine by eliminating the determined wear.
“Improvement” instruction — Continuous improvement of weaknesses in accordance with the Recommendations from the Cooling Lubricant Manufacturer). Refer to our table in the Random Offering Log for this.
4.2 Quality assurance
The prerequisite for the quality assurance requirements is that the product is used in accordance with the contract and the maintenance work and repair work specified by the machine tool manufacturer are performed in accordance with the operating instructions. In addition, all inspections should be carried out by the manufacturer of the machine tool or by personnel authorized by the manufacturer of the machine tool at the specified time interval.
All activities should be recorded in the machine log and should be confirmed by our company.
Machine log should be placed next to each machine.
The machine tool inspection of our company. shall be carried out in accordance with the machine equipment.
4.3 Security
All maintenance work, inspection work and maintenance work can only be carried out by personnel who meet the qualification level of the machine tool factory. The sections “Safety Cautions” and “Warning Notes” should be followed prior to the conduct of hazardous activities.
4.4 Lubricant
4.4.1 The minimum requirements
The following grades of lubricant are allowed:
In line with International Standard |
In line with DIN German Standard |
· Transmission fluid L-CKC In line with International Standard ISO 12925-1 |
· Lube CLP Complies with German Standard DIN 51517, part 3 |
· Hydraulic oil L-HM In line with International Standard ISO 11158 |
· Hydraulic oil HLP/HLP-D In line with German Standard DIN 51524, Part 2 |
· Grease KP In line with International Standard ISO L-X BCH B2 |
· Grease KP In line with German Standard DIN 51825 |
The use of HLP-D oil has advantages when water cannot be excluded from entering hydraulic oil. These oils must meet the minimum requirements of International Standard or German Standard for hydraulic oil HLP. The anti-emulsification ability is an exception. In addition, this oil must be clean.
The detailed technical specifications for lubricants are for each maintenance and maintenance and are described in the section “First Refueling”.
4.4.2 Use of alternative lubricant products
Alternative products are available, except for liquid lubricants of the GP000 class, which shall be subject to the corresponding German Standard/ International Standard grades and viscosity grades, and meet the “first refueling machine tool” standard. It should be ensured that different products are not allowed to be mixed.
The replaceable product must be approved in writing by the alternative lubricant supplier. The prerequisite for machine tool manufacturing plants is that, at least on first use, should be rigorously evaluated by the alternative lubricant supplier so that remedial measures can be managed in a timely manner in the event of a problem.
It should be recorded when changing lubricant products. A table in the log is randomly provided for this reference.
4.5 Lubrication
4.5.1 Basic description
In accordance with the central viscosity at 40°C, the International Standard Classification is based on the nomenclature of viscosity liquid lubricants in German Standard DIN ISO 3448.
This lubrication plan is based on the German Standard DIN 8659.
4.5.2 Symbols in lubrication diagram
Symbols |
Functions |
|
Check the level, add add. |
|
Replace Media, Quantity Description |
|
Discharge medium. |
|
Lubricated with grease |
|
Lubricate with oil. |
|
Clean filter, discharge water (pneumatic) |
|
Replace the filter. |
|
Replace components. |
|
The lubricating oil complies with the Standard DIN 51 517-3. |
|
Hydraulic oils conform to DIN 51 524 Part 2 |
|
Coolant |
|
Cooling lubricant |
![]() |
Dilute grease DIN 51826 |
|
Maintenance Cycle/Running Hours. |
|
See |
4.5.3 Lie and chained type tool magazine with 40T (Standard)
4.5.3.1 Lubrication chart
3. 20000 rpm oil and gas lubrication deit* 4. Filter of pneumatic unit
5. Hydraulic station device 6. Central Lubrication
7. Flip round table (manual or synchronous)* 8. Cooling lubricant box
* Specific configuration according to machine
4.5.3.2 First injection of pump station fuel tank
Different properties and chemical components of dilute grease.
Mixing dilute grease from different manufacturers may cause machine damage.
Only use the first injection of dilute grease from our company to refill the concentration lubrication pumping station.
Symbols |
Adds |
Refueling location |
Manufacturer |
|
Hydraulic oil HLP/HLP-D 46 |
Hydraulic Pumping Station |
FUCCHS RENOLIN ZAF 46 D |
|
Lubricant CLP 68 |
Lubrication station-motor spindle |
FUCCHS RENOLIN CLP 68 |
|
Lubricating oil NBU15 |
Tool Magazine |
KLUBERNBU15 |
|
Dilute grease |
Central Lubrication |
Divinol Fett L800 |
|
Dilute grease |
Rotary table bearing |
KLUBERNBU15 |
![]() |
Coolant MAINTAIN FRICOFIN LEC-15 without water |
Cooling station |
FUCHS MAINTAIN FRICOFIN LEC-15 |
![]() |
Cooling lubricant |
Cooling lubricant box |
Determined by the user. Please value the coolant lubricant section. |
* According to machine configuration
4.5.4 Disc type tool magazine with 24Tand Vertical chained type tool magazine with 40/60T (Option)
4.5.4.1 Lubrication chart
Hydraulic station device 4. 20000 rpm oil and gas lubrication deit* 5. Central Lubrication
6. Flip round table (manual or synchronous)* 7. Cooling lubricant box
* Specific configuration according to machine
4.5.4.2 First injection of pump station fuel tank
Different properties and chemical components of dilute grease.
Mixing dilute grease from different manufacturers may cause machine damage.
Only use the first injection of dilute grease from our company to refill the concentration lubrication pumping station.
Symbols |
Adds |
Refueling location |
Manufacturer |
|
Hydraulic oil HLP/HLP-D 46 |
Hydraulic Pumping Station |
FUCCHS RENOLIN ZAF 46 D |
|
Hydraulic oil HLP/HLP-D 22 |
Lubricator* |
FUCCHS RENOLIN ZAF 22 B |
|
Lubricant CLP 68 |
Lubrication station-motor spindle |
FUCCHS RENOLIN CLP 68 |
|
Lubricating oil VG 150 |
Tool Magazine
|
SHEEL OmalaEP ISO VG150~220 |
|
Dilute grease |
Central Lubrication |
Divinol Fett L800 |
|
Dilute grease |
Flip round workbench (Flip round workbench for manual and synchronized only) |
KLUBERNBU15 |
![]() |
Coolant MAINTAIN FRICOFIN LEC-15 without water |
Cooling station |
FUCHS MAINTAIN FRICOFIN LEC-15 |
![]() |
Cooling lubricant |
Cooling lubricant box |
Determined by the user. Please value the coolant lubricant section. |
* According to machine configuration
4.6 Cooling lubricant
4.6.1 Overview
The following instructions comply with the documentation
"Standard 3.9 / Cooling Lubricant" stipulates.
4.6.1.1 Concept
Cooling lubricants are materials used for cooling and lubrication during chip processing of materials with a specified or unspecified cutting edge or during shape change processing. (DIN 51385)
The water-soluble cooling lubricant should be mixed with water before use. This can be a solution or emulsifier.
- Emulsion (cooling lubricant containing mineral oil or ester oil) contains substances (mainly emulsifiers) that can form a stable emulsion with water.
- The solution (cooling lubricant without mineral oil) consists of water-soluble substances, such as glycol.
- The non-water-soluble cooling lubricant consists of mineral oil or ester oil.
- Both water-soluble and non-water-soluble cooling lubricants contain additives for improving properties, mainly:
- Sulfur, ester and phosphorus, (because chlorine is easy to form acid and residue, it will not be used in the future).
- Sterilizers, rust antiseptics.
- Defoamer
- A substance used to stabilize the pH value.
- Anti-rust additives used to temporarily prevent machine tool rust in water-soluble cooling lubricants.
4.6.1.2 Application of cooling lubricant
The cooling lubricant is hereinafter referred to as KSS for short.
Non-compliance with accident prevention regulations.
- Work on KSS equipment must comply with local labour protection regulations and accident prevention regulations, especially in Germany with BGR (Occupational Insurance Federation Safety and Health Regulations) 143!
- Ambient temperature:
- The specified working temperature of the machine is 15°C to 35°C. If temperature conditions do not match, such as tropical climate packages and cooling lubricant equipment with thermostatic treatment!
- In order to achieve the highest accuracy, the temperature should be kept constant during processing (see also the precautions in this operation manual). When higher precision is required, it is recommended to perform constant temperature treatment on KSS.
- Dirty KSS:
- KSS can shorten its service life when it is dirty.
- Never bring in chemicals, impurities or trash.
- Humid condition:
- Humidity must be avoided as it can prompt rust. Therefore, when the machine stops using, you should open the processing area door and operating door in order to give the machine ventilation.
- Work on KSS related work:
- Wearing the necessary protective supplies when doing work related to KSS! Be aware to comply with the processing requirements of KSS and secure data forms.
Warning! Material with a risk of explosion!
Use KSS with a flammable liquid that accounts for more than 15% by volume.
There is a risk of injury, and fire, explosion or microburst may cause death or serious injury.
- Additional comprehensive explosion protection measures or special optimization measures for the machine are required.
Warning! Material with a risk of explosion!
When processing light metals and light alloys, especially when metals or alloys contain magnesium, can generate spontaneous or explosive particles.
There is a risk of injury, and fire, explosion or microburst may cause death or serious injury.
- Additional comprehensive explosion protection measures or special optimization measures for the machine are required.
4.6.1.3 Selection and maintenance of cooling lubricants
Only by selecting the right KSS and maintaining it professionally can ensure that there is no problem.
Use boron-containing KSS.
According to the current level of inspection (2013 research project), the use of KSS containing boron is suspected of the possible formation of glossy spots on the linear guide.
- If the boron content in the KSS used is> 0.3%, you must check whether the product can be replaced with a product with a lower boron content. Please consult the KSS manufacturer for this.
- If you cannot avoid using KSS with boron content > 0.3%, we recommend that you refer to your documented field experience.
Please ask the KSS supplier to confirm that he has experience in using KSS with confidence on the machine. Such experience is, for example, the experience of using this KSS on a machine tool of the same or similar model of our company or on a machine tool with a similar lubrication system.
Our company is not responsible for machine damage caused by excess of the maxi
mum boron concentration of KSS.
The selection and maintenance of KSS is the responsibility of the machine tool operator!
- Attention must be taken to comply with the requirements set out in the chapters “Water-soluble Cooling Lubricant” and “Non-Water Soluble Cooling Lubricant” by our company.
- KSS must comply with the law and the latest regulations of the Occupational Insurance Federation. In addition, local legal regulations must be observed (in Germany, for example, the Technical Guidelines for Hazardous Goods TRGS 611, the Hazardous Goods Regulation, the Biological Materials Regulation, the Industrial Safety Regulation and BGR 143).
- Please ask the KSS supplier to confirm in writing that the KSS used meets the regulations in terms of concentration! Important factors in ensuring production quality and environmental protection are mainly:
- The content of mineral oil and synthetic oil.
- Water hazard level.
- Additives added.
- It is suitable for all processing methods and the necessary commonality of materials.
- does not hurt the skin.
- KSS should be environmentally friendly and harmless to the workplace.
The selection and maintenance of KSS is the responsibility of the machine tool operator!
The selection and maintenance of KSS is the responsibility of the machine tool operator!
The selection and maintenance of KSS is the responsibility of the machine tool operator!
The selection criteria for KSS are only physical chemistry as well as microbiology guidelines and properties. Therefore, there is no need to consider how to determine the product.
Inapplicable or inadequately tested KSS.
Components and parts that come into contact with KSS can be damaged, such as the supply pump and seals.
Only after long-term testing can the new KSS be approved.
Our company does not assume any responsibility for machine tool damage and functional limitations caused by machine tool operators during processing.
This includes, in particular, the following cases:
- Use of inappropriate KSS.
- Insufficient or incorrect maintenance of KSS.
- Use of inappropriate blended water.
- In case of problems, please contact the KSS supplier.
4.6.2 Water-mixed cooling lubricant
4.6.2.1 Specification on cooling lubricant
It should be noted that only cooling lubricants that meet and fit the requirements listed in this table can be used, and the cooling lubricant must be able to flow through a filter device with a 25 µm filter. This limit is suitable for application concentrations.
Serial number |
Parameters/detection methods |
Restrictions |
Unit of measurement |
1 |
Anti-corrosion: Ash cast iron chip filter testing including additional extensions. |
There was no corrosion after 2 hours. No corrosion after 12 hours. No corrosion after 24 hours. |
Score 0 Score 0 Score 0 |
2 |
Paint compatibility: grid cutting inspection, round mandrel bending inspection |
No erosion of paint. No cracks at 45°C. |
coefficient 0... 1 |
3 |
Elastomer (synthetic rubber) compatibility |
Maximum change in Shore hardness A +/- 10%, maximum +/- 10% dip, or shrinkage. |
|
4 |
Microbial stability. |
According to product technical requirements and manufacturer's regulations. |
Side notes |
5 |
Non ferrous metal compatibility |
Do not corrode copper, brass and aluminum parts, mainly in discoloration and the formation of corroded surfaces. |
|
6 |
The viscous residue characteristics after being concentrated by slow evaporation at 70°C. |
Non bonding! Slight residual solubility or re-emulsification. |
|
7 |
Foam characteristics: The rotating speed is 20000 1/min. Test tube disperser with air inlet. |
The 500 ml beaker did not overflow. |
|
Explanation of numbering.
- Corrosion protection characteristics are tested in accordance with the gray cast iron chip testing of the German Standard DIN 51360 Part 2. In this German Standard DIN-method, it is expected that the reading will be taken after one hour. If there is a deviation from this, the filter paper should be evaluated after 1 hour and 12 or 24 hours. The evaluation criteria are based on the German Standard DIN 51360 Part 2.
- Cooling lubricants should be exposed to a temperature of 50°C for 14 days without damaging their coating characteristics when inspecting grid scratches in accordance with the German Standard DIN EN ISO2409. In addition, the Brinell indentation hardness of paint (DIN EN ISO 2815) should not change negatively. According to the German Standard DIN EN ISO1519 in the round bar bending test (2 mm), a sheet with a coating of 0.7 mm should not be cracked when it is bent to 45°C.
- According to German Standard DIN 53505, the value of Shore hardness A is allowed to change by +/-10% at the maximum. According to German Standard DIN ISO 23529, the maximum permissible change in straight line size is +/-5%. (14 days of operation at 50°C)
- Analysis, conservation measures and the addition of maintenance chemicals are often uneconomical when machining machines come with their own supply of cooling lubricants, so cooling lubricants used for this type of equipment should show proper basic configuration and stability from the beginning. For example, it can be confirmed by cycle testing. To assess the stability of microorganisms should be used DIP Slides (Infringent Agar Tablets) (see www.bode-chemie.com - "bode_dip_slides.pdf" for this).
- Use the German Cooling Lubricant Federation VKIS No. 7 work page to test (determine the corrosive effect of water-mixed products on copper; please refer to the website www.vkis.org) to evaluate electrolytic copper, brass or aluminum strip samples The surface of non-ferrous metals is quantitatively evaluated. Cooling lubricants should contain non-ferrous metal corrosion inhibitors.
- Refer to the German Cooling Lubricant Federation VKIS No. 9 work page for this test (evaluate cooling lubricant (tank bottom) deposits and check residual solubility). In this test, the mixture of 20g of 5% (weight percent) cooling lubricant and user's water is evaporated and concentrated. The adhesive properties will be described in three states, (1) "bonded" (pulling out the filament), "fixed" (paint-like film), or "non-bonded". The bonding effect should be as weak as possible. Please note that too strong bonding effect can negatively affect machine function, especially during prolonged machine outage.
- Add 300 ml of cooling lubricant to a 500 ml beaker. No liquid should overflow after 60 seconds of mixing. The test is suitable for determining the trend of forming foams and comparing the stability of the cooling lubricant foam. A “soda effect” can be obtained in an extended detection (determining trends by bubble bursting). Cooling lubricants with inadequate foam properties or cooling lubricants - working solvents can be easily identified.
If an individual limit value is exceeded during the described test, we recommend to consult with the cooling lubricant supplier, because in many cases one countermeasure is sufficient to solve the problem and can thus avoid the replacement of the entire cooling lubricant.
2.6.2.2 Technical parameters of mixed water
In addition the valid regulations and limits of the local water resources government administration should be observed.
Serial |
Parameter |
Restrictions |
Unit of measurement |
1 |
Total hardness |
5 - 20 Recommended 8 - 12 (0,9-3,6) |
°DH (German Hardness) (mMOL) |
2 |
PH-value |
7 +/- 1 |
pH |
3 |
Conductivity |
Max 700 |
US (Mikro Siemens) |
4 |
chloride |
Max 30 |
ppm |
5 |
Bacteria breeding |
10² |
KBE |
Explanation of numbering.
- Please clarify the best water conditions with the cooling lubricant-supplier, and take corresponding measures according to the actual situation. When there is deviation, saponification may be caused by too hard water or foam may be formed when water is too soft. Please have cooling lubricants suppliers confirm these limits in writing.
- In the event of deviations, please be sure to negotiate with the cooling lubricant supplier about the possibility of water preparation and implement the required measures.
- If the conductivity of the formulated water is already above standard, there is an increased risk of corrosion. Appropriate preparations for water treatment must be taken.
- When the chlorine content is higher, there is a greater risk of corrosion, so it is necessary to properly prepare water.
- The mixed water should show drinking water quality, otherwise it will increase the risk of microbial invasion and corrosion. Problems often arise due to improperly maintained water preparation treatment equipment. Please consult with the cooling lubricant supplier on this.
4.6.2.3 Mixing of cooling lubricants
Please note the description of corrosion prevention in the manufacturer's product data page. The recommended concentration must be followed.
In order to make emulsions, a stirring mixer should be used. In all cases, only slowly mix the cooling lubricant-concentrate with the mixing water.
The cooling lubricant is mixed incorrectly.
Property damage due to corrosion of parts and components in contact with cooling lubricants, e.g. damage to cooling lubricant equipment and chip conveyor containers.
- Only allow the machine's cooling lubricant equipment to be injected with a mixed emulsifier.
- Note that pure water is not allowed, otherwise it will be below the minimum concentration. (In accordance with the technical specifications in the section "Technical Parameters of Mixed Mixed Water")
- The emulsifier can only be kept in suitable containers. Contact the manufacturer if necessary.
Attention should be paid to the mixing temperature.
The temperature difference between the concentrated cooling lubricant and the adhesion water during mixing is not allowed to exceed 10K. The minimum temperature of concentrated cooling lubricant and adhering water is 10°C, and the maximum temperature during mixing must not exceed 30°C.
4.6.2.4 Supplemental addition and replacement of cooling lubricant
The correct concentration of coolant lubricant should be added in a timely manner if necessary.
In this regard, it is essential to determine the emulsion concentration in the machine cooling lubricant circuit. Monitoring once a day will prevent undetected changes in concentration.
Please note that the concentration composition may change through vaporization and loss with the workpiece.
As the use time increases, the technical characteristics of the application of cooling lubricants will also change. This is also known as aging. If appropriate measures (for example, the use of calibrators) cannot stop this Process, partial or complete replacement is necessary. Please consult with the cooling lubricant supplier.
Suggestions for cleaning
Please note that machines that are not thoroughly cleaned will greatly reduce the life of cooling lubricants (e.g., via contaminants or flora generation) after the new injection.
24 hours before the planned replacement, add 1-2% system decontaminant to the old cooling lubricant (please consult with the cooling lubricant supplier for details). In order to reach all contaminated areas, the highest liquid level that meets the operational requirements must be generated in the machine tool. To make the system purifiers evenly distributed, continue to run the machine tools or let the cooling lubricants operate in a circulating flow manner. The emulsifier is discharged after about 24 hours and thoroughly clean the processing area, chip conveyor and cooling lubricant unit. Therefore, flush the machine tool at the same filling volume with circulating diluted cooling lubricant (about 1%), such as flushing with a system decontaminant. The residual amount of preservative and dissolved contaminants should be removed while maintaining the system decontaminant.
System Cleaner
Wrong system purifier.
Property damage is caused by corrosion of parts and components exposed to the purifier, such as the housing of cooling lubricant equipment and chip conveyor.
Do not use pure water for cleaning.
Please use the system purge agent determined by the cooling lubricant and pay attention to its application regulations. Please also consult with the cooling lubricant supplier on this.
Cleaning effect:
The selected system purifier should stay in the cooling lubricant system for about 24 hours and then follow the recommended concentration. The cleaning effect should be obvious.
This system purifier is not a substitute for mechanical cleaning in case of severe contamination of machine tools and cooling lubricant systems!
New addition of cooling lubricant
Always fill the machine with diluted cooling lubricant (approx. 1%) before filling with cooling lubricant and flush for at least one hour; otherwise there is a risk of shortened life and/or foam formation during subsequent re-use.
Waste disposal
Recycling and disposal of used cooling lubricants according to local regulations! The safety data page for cooling lubricants contains relevant precautions.
4.6.2.5 Monitoring and documentation
In order to ensure the function of the machine/equipment, the cooling lubricant must be periodically tested.
Our company suggests that the number of inspections should be determined together with the cooling lubricant supplier, because the number of inspections is greatly affected by environmental conditions and processing tasks.
If the user's company does not have the necessary test equipment, the test can only be carried out by an independent test laboratory or by the cooling lubricant supplier.
This test result must be archived and given to the after-sales technician of our company upon request. (See TRGS 611)
Parameter |
Parameter |
Measuring method/measuring agent |
Cycle (standard) |
Scheduled |
1 |
Concentration |
Refractive Checker |
Once a day |
According to the manufacturer's instructions. |
2 |
PH-value |
A combination test paper with 0.2- as a block in the important range. |
Once a week |
The pH-value range recommended by the cooling lubricant manufacturer. |
3 |
Nitrite |
Combination test paper 0 - 80 ppm. |
Once a week |
For example, up to 20 ppm (used in Germany). |
4 |
Chloride |
Max 100 |
once a month |
ppm |
5 |
Total hardness |
Combined test paper 0 - 30°DHC. |
once a month |
Min 7°dH to Max 30°dH |
6 |
Fungal breeding |
For example, immersion medium (invasive agar glass) and visual evaluation. |
Once a month, once a week if necessary. |
According to the manufacturer's instructions. |
7 |
Bacteria breeding |
For example, immersion medium (invading agar glass. |
Once a month, once a week if necessary. |
According to the manufacturer's instructions. |
8 |
Temperature |
Thermometer |
Once a week |
Max 35C |
9 |
Conductivity |
Measuring electrode |
Once a week |
Up to 4000µS |
Explanation of numbering.
- The manufacturer of the cooling lubricant has given the required concentration for use. There must be emphasis on never allowing conditions below or above that tolerance limit, otherwise there will be other corrosion hazards. Please note that in general the level should not fall below the minimum level (see chapter "Maintenance").
- If the limit values specified by the cooling lubricant supplier are exceeded or lowered, it is important to discuss suitable stabilization measures with the cooling lubricant supplier.
- If the specified limit value (currently 20 ppm is used in Germany) is exceeded, there are the following possibilities to solve the problem:
- Replace part of the cooling lubricant.
- Replace all cooling lubricants.
- Detect the content of nitrosamines in cooling lubricants and working gas.
- Exceptions to TRGS 611 are obtained.
- The total hardness greater than 30°dH (5.4 mMoL) can lead to stability and corrosion problems. Total hardness below 7°dH (1.25 mMoL) will often trigger foam problems. Please contact the supplier of the cooling lubricant and give the deviating values in writing if necessary, or ask the supplier to recommend another cooling lubricant.
- Fungal growth in cooling lubricants can be related to corrosion problems, foaming problems, or even major problems. Therefore, the presence of impermissible enzyme bacteria contamination in the system is not allowed. It is important to detect areas where enzyme bacteria can easily grow, such as the four walls of the vessel, piping, cooling lubricant pumps and filter unit dispensers/inlet plates. When slimy moss appears in these areas, there is a major suspicion of fungus production. Unfortunately, since the introduction of an intrusive medium (Dip-Slides) is not particularly convincing for the presence of fungi, additional visual examination is essential. In the big cooling lubricant - the system adopts preventive antiseptic treatment is economical. The fungicide content should be monitored regularly (at least 14 days) using laboratory technology and cooling lubricant should be added when necessary. Such analysis tests should be carried out by the cooling lubricant manufacturer or a neutral testing organization.
- It is important to note that there are also slow-growing colonies and anaerobic bacteria, which are not recognized with traditional immersion cultures. A pilot analysis is provided here for a large cooling lubricant system, after which the biocide content is determined and specified, what amounts have been consumed and how much additional is to be added. These analysis tests should be carried out by the manufacturer or a neutral testing organization.
- If the temperature in the cooling lubricant tank exceeds 35°C, we recommend controlling the temperature of the cooling lubricant.
- Corrosion problems may occur when predetermined values are exceeded and cause the emulsion to break down into water and concentrate. When the above temperature is exceeded, please consult with the cooling lubricant supplier in time.
4.6.2.6 Help with problems
Corrosion of machines, tools and workpieces
Possible Causes |
Troubleshooting |
Condensate formation |
Machine tool ventilation change (open the machining area door and operating door). |
Since there is a foreign body PH-value will drop. |
Please check the pH-value, add a pH-value-stabilizer if necessary; prevent foreign matter (such as oil, germs) from being invaded. |
Reduce cooling lubricant concentration. |
Please check the concentration and increase the concentration if necessary. Please use a stirring mixer, please pay attention to complying with the mixing rules. |
Increase hardness, or increase salt content. |
The total hardness of the cooling lubricant should be tested, and if necessary, use VE-water* to resist. |
Digestion or segregation of anti-corrosion additives. |
According to the German Standard DIN 51360 Part 2, check the corrosion protection, increase the concentration of the cooling lubricant or replace it if necessary; check the adjustment of the centrifuge used when necessary. |
Outer oil |
Remove by taking appropriate measures, for example, using a device for skimming slick oil or a foreign oil separator. |
Mechanical damage is caused by corrosion through emulsifying liquid. |
Please check the pump and piping. |
* (In technical VE-water one understands 0°dH fully salted water (0.2 mmol calcium) and a maximum conductivity of 20 µS.)
Work pieces (aluminum, copper, brass) and machine tool parts discoloration
Possible Causes |
Troubleshooting |
Decomposition or consumption of non-ferrous metal corrosion inhibitors or improper cooling lubricants (not containing non-ferrous metal inhibitors). |
Add non-ferrous metal corrosion inhibitors or use other cooling lubricants with metal inhibitors. |
germ-/mold infestation; bad odor burden
Possible Causes |
Troubleshooting |
Digest the antimicrobial agent or bring in foreign matter (in the cooling lubricant containing the antimicrobial agent). |
The condition of microbial contaminants in cooling lubricants should be checked regularly or biological analysis should be carried out. Please contact the coolant lubricant supplier. |
Outer oil |
By taking appropriate measures to clear, allow the cooling lubricant to circulate flow even when the machine is down, with compressed air if necessary (up to 0.5 bar) Ventilate during machine shutdown, use oil skimmer or oil separator. |
Deteriorating emulsion or solution condition. |
Introduce maintenance measures. |
Shorten tool life, poor machining surface and corrosion
Possible Causes |
Troubleshooting |
Consumption of performance components, oil content and additive content. |
The cooling lubricant should be concentrated if necessary; the concentration should be determined according to the total oil content in agreement with the cooling lubricantsupplier and should be compared with the acid titration concentration of the refractometer. Please check the filtration (hydrocyclones must not be used.) |
Mis-tuned centrifuges will lead to cooling lubricant - deprivation of components. |
Match the adjustment if necessary. |
Cooling lubricant supply is insufficient. |
The pump power and nozzle debugging shall be checked. |
Reduced lubrication performance by foam. |
See the section on bubble issues. |
Cooling lubricant (bottom of the tank) deposits on the machine tool
Possible Causes |
Troubleshooting |
Foreign oil (poor rinse characteristics, adhesion). |
Appropriate maintenance devices should be used, such as an oil skimmer or a contaminant oil separator for removing the closed oil cap. foreign oil compatibility test, Partially replace the cooling lubricant if necessary. |
Increase hardness, or increase salt content. |
Please check the total hardness of the cooling lubricant, and if necessary, use technical conditioning to neutralize it. |
Foam formation
Possible Causes |
Troubleshooting |
The total hardness of the emulsion is too low. |
Please consult with cooling lubricant supplier to increase the hardness of the coolant lubricant if possible. |
Contamination by foreign substances (e.g., cleaning agents). |
Partially replace (at least 50%) the cooling lubricant. |
The cooling lubricant concentration is too high. |
Reduce the concentration of emulsion with the right water quality. |
Unsealing (pump) in the circulation loop. |
Causes of failure that should be eliminated. |
Filtering problems
Possible Causes |
Troubleshooting |
Mold infestation |
Mechanical cleaning. After consultation with the cooling lubricant manufacturer, the appropriate fungus should be used, and it is important to adhere to the prescribed dosage. |
4.6.3 Non-aqueous hybrid cooling lubricant
4.6.3.1 Specification of cooling lubricant
Warning! Material with a risk of explosion!
When combustible oil is used as a cooling lubricant, explosive cooling lubricant-vapor-aerosol-air mixtures may be generated in the machining room of the machine tool.
Injury accidents may occur through fire, explosion or spark deflagration, and may result in death or serious personal injury.
- In the absence of special fire fighting equipment. For safety reasons (explosion hazard), cooling lubricants (cutting oils) that cannot be mixed with water are not allowed.
- When processing is used, it must have, and the monitoring system of the fire extinguishing device must be activated.
Only use cooling lubricants with the following characteristics:
- Flashpoint > 140 C meets International Standard ISO 2719 (Pan-Marmite Closed-Cup Flash Point Test Method).
- Evaporation loss <5% (according to German Standard DIN 51581-1 at 150 ℃).
- Viscosity> 8 mm²/s (according to German Standard DIN 51562 at 40 ℃).
The following features are further recommended.
- The lower limit of explosion should be greater than 25 g / m³.
- Maximum explosive pressure is 8 bar.
- The pressure increase per millisecond during the explosion should be less than 100 bar.
- Cooling lubricants should contain anti-fog additives.
The cooling lubricant must be compatible with the lubricant and hydraulic oil used in the machine tool. Please pay attention to the lubricant used for the first filling, and consult with the cooling lubricant supplier on this.
In addition, it should be noted that only cooling lubricants that comply with the regulations listed in the table and are compatible with the materials used on the machine tool can be used. The cooling lubricant must be suitable for flowing through a filter device with a 100 µm filter.
Serial |
Parameters/detection methods |
Restrictions |
Unit of measurement |
1 |
Paint compatibility: grid cutting inspection, round mandrel bending inspection |
No erosion of paint. No cracks at 45°C. |
coefficient 0... 1 |
2 |
For compatibility of elastomers (synthetic rubber), please refer to paint inspection for explosive conditions. |
Maximum change in Shore hardness A +/- 10%, maximum +/- 10% dip, or shrinkage. |
|
3 |
Non ferrous metal compatibility |
Non-ferrous metals that are discolored due to erosion and form films are not allowed. |
Index 1 (only for copper) |
Explanation of numbering.
- The cooling lubricant should be exposed to 50°C for 14 days. A grid cut test in accordance with the standard DIN EN ISO 2409 shows that the properties of the coating have not deteriorated. In addition, the Brinell indentation hardness of paint (DIN EN ISO 2815) should not change negatively. According to the German Standard DIN EN ISO 1519 in the round bar bending test (2 mm), a sheet with a coating of 0.7 mm should not be cracked when bent to 45°C.
- According to German Standard DIN 53505, the maximum allowable change in Shore hardness A value is +/-10%. According to German Standard DIN ISO 23529, the maximum permissible change in straight line size is +/-5%. (14 days of action at 50 °C).
- Copper-corrosion test according to Standard DIN EN ISO 2160.
4.6.3.2 Provisions on processing and machine tools
Blunt, broken blade or wrong rapid cooling.
Coolant lubricant combustion hazards due to fog on the blade or the formation of sparks.
- Adjusts the coolant lubricant nozzle to optimum condition to rinse the processing area and avoid chip build-up.
- A sufficient amount of cooling lubricant should be supplied to prevent sparks from forming on the blade.
- Cooling lubricant supply must be monitored.
- The temperature of the cooling lubricant must also be monitored.
- Suction devices suitable for oil processing (electrostatic) must be installed.
- Blunt and non-fogging oil should be used (see the recommendations of the Industrial Injury Insurance Federation on fire and explosion protection).
Explosion-proof kit is needed!
For machine tools that cannot be optimized to the above parameters, an additional explosion-proof package must be installed.
4.6.3.3 Supplemental addition and replacement of cooling lubricant
Added in a timely manner.
Be sure to ask for timely additions.
If the technical characteristics of the cooling lubricant cannot be maintained economically (for example, due to contamination, aging), the cooling lubricant must be replaced. Please consult with the cooling lubricant supplier.
Recording is required when the cooling lubricant is replaced or added. (See the section "Monitoring and Archiving Records")
Suggestions for cleaning
Please note that a machine that is not thoroughly cleaned will shorten the life of the cooling lubricant (for example, in pollution), or may reduce cutting capacity.
Before emptying, the cooling lubricant should be circulated for at least one hour or circulated with a pump to avoid contaminated esters. Pump out the old cooling lubricant directly after this, preferably drawn from the coolant lubricant unit as deep as possible.
New addition of cooling lubricant
Rinse with new product.
- When the composition is greatly changed after being heavily contaminated or after long-term use, a new product should be used for washing.
- The amount of cooling lubricant used for flushing is then recovered and disposed of.
- The need for such a flush operation can be derived with the help of analytic data.
- If it is contaminated by a large amount of incompatible foreign matter (for example: concentrate, glycol, water, solvent, cleaning agent), if necessary, special measures should be taken to ensure that the foreign matter is completely removed from the circulation system.
- Please consult with the cooling lubricant supplier to avoid damage to the machine tool or performance degradation during cutting.
Waste disposal
Recycling and disposal of used cooling lubricants according to local regulations! The safety data page for cooling lubricants contains relevant precautions.
4.6.3.3 Monitoring and documentation
In order to ensure the function of the machine/equipment, the cooling lubricant must be periodically tested.
Because this is greatly affected by environmental conditions and processing tasks, I recommend working with the cooling lubricant - supplier to determine the frequency of inspections.
When the necessary equipment is not available in the company, this test can be performed by other laboratories or by cooling lubricants - suppliers.
This test result must be archived and given to the after-sales technician of our company upon request.
“Improvement” Description — Continuous improvement of weaknesses in accordance with BVW (Recommendations for cooling lubricant manufacturers). Refer to our table in the Random Offering Log for this.
Serial |
Parameter |
Measuring method/measuring agent |
Cycle (standard) |
Scheduled |
1 |
Viscosity (40°C) |
DIN 51562 |
monthly |
According to manufacturer's instructions (mm2/s). |
2 |
Water content |
DIN EN ISO 12937 |
monthly |
Increase when compared to the original product <300 ppm 。 |
3 |
Phosphorus, sulfur, zinc, calcium, sodium, copper, chlorine |
ICP (inductively coupled plasma) or X-ray fluorescence. |
This period is determined in consultation with the cooling lubricant supplier. |
<20% deviation when compared with the original product. |
4 |
flashpoint |
Pan-Marmite Closed-Cup Flash Point Test Method. |
When necessary. |
>140°C conforms to International Standard ISO 2719 |
Explanation of numbering.
- When the viscosity changes significantly (+/- 20%), please check whether there is foreign oil from the machine tool or the workpiece. This may have an adverse effect on the filtration and/or processing procedures, for example. Partially replace the cooling lubricant when necessary.
- If that limit is exceeded, then negotiate with cooling lubricant supplier to take appropriate stabilization measures, for example, with the appropriate absorbent treatment or partial replacement. (see Karl-Fischer measurement method)
- When determining the flash points, the decrease of solution odor and/or viscosity implies that there is serious foreign body infestation.
4.6.3.5 Help with problems
Corrosion of machines, tools and workpieces
Possible Causes |
Troubleshooting |
The hazards of water-mixed cooling lubricants or cleaning agents. |
Please check the workpiece and clean it if necessary; partially replace the cooling lubricant if necessary. |
Shortened tool life and poor surface quality
Possible Causes |
Troubleshooting |
The additive content is too low. |
Add wear-resistant additives. |
The harmful nature of foreign oil or grease. |
If necessary, replace part of the cooling lubricant. |
The viscosity of the cooling lubricant is too high or too low. |
If necessary, replace part or all of the cooling lubricant. |
The alloy material of the workpiece is changed. |
Please check the workpiece material |
Foam formation
Possible Causes |
Troubleshooting |
The hazard of foreign objects. |
Use short-term defoaming agent; Partially replace the cooling lubricant if necessary. |
Liquid level too low. |
Add a cooling lubricant. |
The cooling lubricant-circulation circuit/pump is not sealed. |
Please troubleshoot the defect. |
Filtering problems
Possible Causes |
Troubleshooting |
The hazard of foreign objects. |
Please check the cooling lubricant-system and the workpiece and clean if necessary. |
The hazards of water-mixed cooling lubricants or cleaning agents. |
If necessary, replace part or all of the cooling lubricant. |
Aging of cooling lubricants. |
If necessary, replace part or all of the cooling lubricant. |
4.6.4 Minimum lubrication
Minimum lubrication is the method that uses no more than 50 ml of lubricant on average per processing hour and processing site (BGR 143). When the process is optimized, the minimum amount of lubrication can increase productivity and contribute to environmental protection.
4.6.4.1 Specifications on the cooling lubricant
Minimum amount lubrication system.
Minimum amount lubrication system is allowed in machine tools with non-water mixed cooling lubricants!
Warning! Material with a risk of explosion!
When combustible oil is used as a cooling lubricant, explosive cooling lubricant-vapor-aerosol-air mixtures may be generated in the machining room of the machine tool.
Injury accidents may occur through fire, explosion or spark deflagration, and may result in death or serious personal injury.
- In the absence of special fire fighting equipment. For safety reasons (explosion hazard), cooling lubricants (cutting oils) that cannot be mixed with water are not allowed.
- When processing is used, it must have, and the monitoring system of the fire extinguishing device must be activated.
Only use cooling lubricants with the following characteristics (see BGR 143):
- Flashpoint > 140 ℃ meets International Standard ISO 2719 (Pan-Marmite Closed-Cup Flash Point Test Method).
- Evaporation loss < 5% (according to German Standard DIN 51581-1 at 150 ℃).
- Viscosity> 10 mm²/s (according to German Standard DIN 51562 at 40 ℃).
Do not use:
- The cooling lubricant that contains organic and chlorine or zinc-containing additives.
- Cooling lubricants marked as meeting hazardous material regulations.
- Mineral crude oil-based products in cooling lubricants contain> 3 ppm benzopyrene.
- Natural esters (rapeseed oil or similar) have a tendency to solidify.
- See BGI 718 for further information.
4.6.4.2 Processing procedures and machine tools
The use of coolant lubricant requires machine tools specially prepared, concerning:
- The air mixing device used to prepare the cooling lubricant.
- The way of conveying the blade.
- Clear the chips.
We are not responsible for machine tool damage caused by machine tool users and performance limitations during processing.
This relates specifically to:
- The cooling lubricant does not meet the cutting parameters.
- The lubrication dosage is incorrect.
- Due to improper processing optimization, problems may occur when removing chips.
- Processing accuracy changes due to insufficient cooling effect of the cooling lubricant.
- If there is a problem, please contact the cooling lubricant supplier.
4.7 Qualification and qualification level of personnel
A summary of what maintenance and repair work can be performed at what qualification level is not yet available for procedural technical reasons.
|
Definition of qualification level |
|
· How to teach the usage of machine tool protection device. · How to teach the use of personal protection measures. · If he understands the task given to him and is taught how to use it if necessary. · How to understand possible dangers when acting incorrectly |
|
· How to train a method of contact with machine tools. · How to understand what's in the action manual about operation and maintenance · If there may be a discretion regarding operation and maintenance, and start or carry out the necessary work. |
|
· If a special qualification is obtained in his field of expertise through training, knowledge and experience. · If you understand machine conditions and hazards in his area of expertise, decide and start or do the necessary work. · If there are related standards of manufacturing*. |
|
· If trained by machine tool manufacturers for repair services and maintenance repairs. · If the qualification certificate is obtained through the training of the machine tool manufacturer. Or a repair service person belonging to a machine tool manufacturing plant. |
|
· If qualified to carry out repair services and maintenance, the repair services and maintenance (such as the use of fire extinguishers) can be carried out by specially qualified persons in accordance with the provisions of third parties or legislators. |
* The concept of limitations of European Standard EN and European Standard EN IEC is not understood here in the concept “relevant standards”, but also other regulations and regulations of the makers.
4.8 Maintenance interva
The time intervals for maintenance, inspection and repair work must be performed according to these time intervals.
If a machine tool inspection or maintenance service agent of our company is performed, the records that match the time interval will be displayed.
- Maintenance intervals are 50, 250, 500, 1000, 2000 hours.
- The inspection interval is every 2000 hours, and the inspection range 1 and 2 are switched.
- All maintenance intervals and maintenance intervals within 50 hours or if necessary must be observed!
Intervals must be matched when the machine load is too large, or when processing large dust materials, such as gray cast iron.
4.9 Maintenance instructions
To clean the machine a fibrous material such as a cleaning rag or similar should be used.
It is strictly forbidden to use compressed air to clean the machine.
4.10 Symbolic description of maintenance work
Symbols |
Name |
Stating |
|
Qualification level |
See paragraph “Qualifications and Level of Qualifications”. |
|
Qualification level: trained person |
See paragraph “Qualifications and Level of Qualifications”. |
|
Qualification level: operator |
See paragraph “Qualifications and Level of Qualifications”. |
|
Qualification level: Professional mechanics |
See paragraph “Qualifications and Level of Qualifications”. |
|
Qualification level : Professional electrical personnel |
See paragraph “Qualifications and Level of Qualifications”. |
|
Qualification level: Maintenance service personnel |
See paragraph “Qualifications and Level of Qualifications”. |
|
Qualification level: People with special qualifications |
See paragraph “Qualifications and Level of Qualifications”. |
|
Time interval |
The display of time interval (unit: hour) should be carried out according to this time interval. The specified intervals: 8, 50, 250, 500, 1000, 2000, specialized intervals. |
|
Page number |
A page description describing the job in detail (only applicable to qualification levels 1 to 3). |
|
Assembly |
The name of the part on which this work should be performed. |
|
Job Content |
A brief description of maintenance and maintenance work. |
|
Division of work scope |
Work is divided into "mechanical" and "electrical" aspects. |
|
Mechanical |
Work on the “mechanical” side. |
|
Electrical |
Work on the “electrical” side. |
|
Operating conditions of machine tools |
Description of the operating condition of the machine tool during work: • The symbol "0" of the power-disconnecting device: · The machine must stop running. • Symbol "1" of power supply-disconnecting device: · Machine tools can be run. |
|
Maintenance category |
Place this in the “Maintenance and Maintenance” category. |
Symbols |
Name |
Stating |
|
Repair category |
Place this work in the category “Warranty Repair”. |
|
Inspection work |
Check job symbol. |
|
Refill coolant |
Refill the symbol of coolant work. |
|
Empty coolant |
Symbol for "Empty the coolant" |
|
Replace/change coolant |
Symbol for "Replace/change coolant" |
|
Cleaning work |
The symbol for cleaning work. |
|
Lubrication work |
Symbol for lubrication work |
|
Tools, materials, production materials |
Marks whether tools, materials, production materials are needed for the job: • Mark "X": · Needed. • Mark "-". · Notnecessary. |
|
Perishable parts |
Mark whether there are wear parts recommendations for this work: • Mark "X": · Wear parts are recommended. • Mark "-". · No consumable parts are recommended. |
|
Milling by machining process |
Marker for "Milling by machining process" |
|
Turning by machining process |
Marker for “Turning by machining process” |
4.11 Maintenance
4.1.1 Whole machine
Maintenance job |
Maintenance period [h] |
||||||
8 |
50 |
250 |
500 |
1000 |
2000 |
According to specific conditions |
|
Cleaning the outside of the machine |
|
x |
|
|
|
|
|
Clean the inside of the machine |
|
x |
|
|
|
|
|
4.11.2 Processing zone
Maintenance job |
Maintenance period [h] |
||||||
8 |
50 |
250 |
500 |
1000 |
2000 |
According to specific conditions |
|
Rear range of processing area |
|||||||
Clearing Chips |
|
|
|
|
x |
|
|
Cleaning the back area of the processing room |
|
|
|
|
x |
|
|
Range in the processing area |
|||||||
Clearing Chips |
|
x |
|
|
|
|
|
Cleaning the processing shop |
|
x |
|
|
|
|
|
Upper range of the processing shop |
|||||||
Clearing Chips |
|
|
|
|
x |
|
|
Cleaning the upper area of the machining room |
|
|
|
|
x |
|
|
4.11.3 Axis
Maintenance work |
Maintenance period [h] |
||||||
8 |
50 |
250 |
500 |
1000 |
2000 |
According to specific conditions |
|
Removal of chips from corrugated box |
|
x |
|
|
|
|
|
Clean the corrugated box |
|
x |
|
|
|
|
|
Clear the chips from steel protective covers |
|
x |
|
|
|
|
|
Clean steel protective cover |
|
x |
|
|
|
|
|
Rail cleaning and oil coating (on oil) |
|
|
|
|
x |
|
|
4.11.4 Viewing glass
Maintenance job |
Maintenance period [h] |
||||||
8 |
50 |
250 |
500 |
1000 |
2000 |
According to specific conditions |
|
Clean windows glass |
x |
|
|
|
|
|
|
Check windows glass for damage |
x |
|
|
|
|
|
|
Determine the ability of windows glass to block impact |
|
|
|
|
|
x |
|
4.11.5 Operation console
Maintenance work |
Maintenance interval [H] |
||||||
8 |
50 |
250 |
500 |
1000 |
2000 |
According to demand |
|
Clean operations console |
|
x |
|
|
|
|
|
Check confirmation and function keys |
|
|
x |
|
|
|
|
4.11.6 Emergency stop device
Maintenance work |
Maintenance interval [H] |
||||||
8 |
50 |
250 |
500 |
1000 |
2000 |
According to demand |
|
Functional check |
|
|
x |
|
|
|
|
4.11.7 Manual emergency unlocking
Maintenance job |
Maintenance period [h] |
||||||
8 |
50 |
250 |
500 |
1000 |
2000 |
According to specific conditions |
|
Function test |
|
|
x |
|
|
|
|
4.11.8 Processing area door
Maintenance work |
Maintenance period [h] |
||||||
8 |
50 |
250 |
500 |
1000 |
2000 |
According to specific conditions |
|
Clean the rails and oil |
|
x |
|
|
|
|
|
4.11.9 Electric control cabinets
Maintenance work |
Maintenance Interval [Hours] |
||||||
8 |
50 |
250 |
500 |
1000 |
2000 |
According to demand |
|
Check joints and connectors |
|
|
|
|
|
x |
|
4.11.10 Hard drive
Maintenance job |
Maintenance period [h] |
||||||
8 |
50 |
250 |
500 |
1000 |
2000 |
According to specific conditions |
|
Commissioned to check hard drives (approximately every 3-5 years) |
|
|
|
|
|
|
x |
4.11.11 Electric control cabinet cooler
Maintenance job |
Maintenance period [h] |
||||||
8 |
50 |
250 |
500 |
1000 |
2000 |
According to specific conditions |
|
Clean shutters |
|
x |
|
|
|
|
|
Check the discharge of condensate. |
|
x |
|
|
|
|
|
Replace filter felt pad |
|
|
|
|
|
|
x |
4.11.12 Hoses and tubes
Maintenance work |
Maintenance period [h] |
||||||
8 |
50 |
250 |
500 |
1000 |
2000 |
6 years |
|
Visual inspection |
|
|
|
|
x |
|
|
Replace the hydraulic line. |
|
|
|
|
|
|
x |
4.11.13 Hydraulic pumping station
Maintenance work |
Maintenance period [h] |
||||||
8 |
50 |
250 |
500 |
1000 |
2000 |
According to specific conditions |
|
Check the liquid level |
|
|
x |
|
|
|
|
Replace oil |
|
|
|
|
|
|
x |
Check nitrogen pressure |
|
|
|
|
|
|
x |
Spare parts and operating consumables required |
Product code |
Hydraulic oil HLPD 46 |
2775584 |
4.11.14 Host buffer batteries
Maintenance job |
Maintenance period [h] |
||||||
8 |
50 |
250 |
500 |
1000 |
2000 |
According to specific conditions |
|
Replace the backup battery |
|
|
|
|
|
|
x |
Spare parts and operating consumables required |
Control system |
Product code |
3V lithium battery |
iTNC/MillPlus |
2298405 |
3V lithium battery |
Siemens |
2254242 |
4.11.15 Pneumatic unit
Maintenance job |
Maintenance period [h] |
||||||
8 |
50 |
250 |
500 |
1000 |
2000 |
According to specific conditions |
|
Check the pressure of the pressure gauge |
x |
|
|
|
|
|
|
Emissions of condensate. |
|
|
|
|
|
|
x |
Replace coarse filter |
|
|
|
|
|
x |
|
Cleaning the filter tank |
|
|
|
|
|
x |
|
4.11.16 Central lubrication device
Maintenance work |
Maintenance period [h] |
||||||
8 |
50 |
250 |
500 |
1000 |
2000 |
According to specific conditions |
|
Check the liquid level |
|
|
|
x |
|
|
|
Spare parts and operating consumables required |
Item number |
Dilute grease: Supplement grease tube DivinolLithogrease 000 lithium-based grease. |
27078178 |
4.11.17 Processing spindle lubrication station
Maintenance work |
Maintenance period [h] |
||||||
8 |
50 |
250 |
500 |
1000 |
2000 |
According to specific conditions |
|
Check the liquid level |
|
|
|
x |
|
|
|
Check the pressure of the pressure gauge |
x |
|
|
|
|
|
|
Replace the filter core |
|
|
|
|
|
|
x |
Spare parts and operating consumables required |
Item number |
Lubricant CLP 68 |
2704048 |
4.11.18 Machine tool heat exchanger
Maintenance work |
Maintenance period [h] |
||||||
8 |
50 |
250 |
500 |
1000 |
2000 |
According to specific conditions |
|
Check the liquid level |
|
|
|
x |
|
|
|
Check the mixing ratio |
|
|
|
x |
|
|
|
Check for dirt and solid matter in the coolant |
|
|
x |
|
|
|
|
Check the tightness of all connections on the equipment |
|
x |
|
|
|
|
|
Check fan exhaust noise |
|
|
|
|
x |
|
|
Clean the filter grille and cooler sheet |
|
x |
|
|
|
|
|
Replace the coolant |
|
|
|
|
|
|
x |
4.11.19 Tool magazine
Maintenance work |
Maintenance period [h] |
||||||
8 |
50 |
250 |
500 |
1000 |
2000 |
According to specific conditions |
|
Cleaning the tool bag |
|
x |
|
|
|
|
|
Lubrication of tool magazine guides |
|
|
|
x |
|
|
|
Clean the feeding auxiliary guide device and apply oil |
|
x |
|
x |
|
|
|
Lubricate the sprocket |
|
|
|
|
x |
|
|
Check chain tension |
|
|
|
|
|
|
x |
4.11.20 Gearbox of tool changer
Maintenance work |
Maintenance period [h] |
||||||
8 |
50 |
250 |
500 |
1000 |
2000 |
According to specific conditions |
|
Check the liquid level |
|
|
|
x |
|
|
|
Replenish lubricants |
|
|
|
x |
|
|
|
4.11.20 Double gripper
Maintenance job |
Maintenance period [h] |
||||||
8 |
50 |
250 |
500 |
1000 |
2000 |
According to specific conditions |
|
Clean double grips |
|
|
x |
|
|
|
|
Spray with metaflux-spray |
|
|
x |
|
|
|
|
4.11.22 Chip conveyor
Maintenance job |
Maintenance period [h] |
||||||
8 |
50 |
250 |
500 |
1000 |
2000 |
According to specific conditions |
|
Check the liquid level |
|
x |
|
|
|
|
|
Check the screen basket and clean if necessary |
x |
|
|
|
|
|
|
Clean chip conveyor |
|
|
x |
|
|
|
|
Replace cooling lubricant |
|
|
x |
|
|
|
|
Check and adjust the tension of the conveyor belt if necessary. |
|
|
|
|
|
x |
|
4.11.23 Spindle taper hole
Maintenance job |
Maintenance period [h] |
||||||
8 |
50 |
250 |
500 |
1000 |
2000 |
According to specific conditions |
|
Clean the spindle taper hole. |
x |
|
|
|
|
|
|
Spray the surface of the spindle taper hole. |
x |
|
|
|
|
|
|
Check for damage |
|
|
|
|
x |
|
|
4.11.24 Tool clamping system
Maintenance job |
Maintenance period [h] |
||||||
8 |
50 |
250 |
500 |
1000 |
2000 |
According to specific conditions |
|
Check claw resizing |
|
|
|
|
x |
|
|
4.11.25 Laser tool measurement
Maintenance work |
Maintenance period [h] |
||||||
8 |
50 |
250 |
500 |
1000 |
2000 |
According to specific conditions |
|
Check the pressure of the pressure gauge |
x |
|
|
|
|
|
|
Check the contamination level of the filter |
|
x |
|
|
|
|
|
Replace filter |
|
|
|
|
|
x |
|
Calibration of grating |
|
x |
|
|
|
|
|
4.11.26 Measuring probe
Maintenance work |
Maintenance period [h] |
||||||
8 |
50 |
250 |
500 |
1000 |
2000 |
According to specific conditions |
|
Replace battery |
|
|
|
|
|
|
x |
Cleaning |
|
|
|
|
|
|
x |
Check wires and connectors |
|
|
|
|
x |
|
|
4.11.27 Flip round table
Maintenance work |
Maintenance period [h] |
||||||
8 |
50 |
250 |
500 |
1000 |
2000 |
According to specific conditions |
|
Lubricate the nozzle with dilute grease |
|
|
x |
|
|
|
|
4.12 Check
These inspections need to change the inspection work every 2000 hours (operation program), according to inspection scope 1 and 2.
4.12.1 Inspection scope 1
After 2000 hours of operation, perform this first inspection according to inspection scope 1.
Repeat inspection according to inspection scope 1, and change inspection according to inspection scope 2.
The time interval for checking scope 1 is 4000 hours.
|
|
|
Pneumatic |
Check the pressure debugging according to the pneumatic system table |
|
Pneumatic |
Visually inspect the automatic water separator |
|
Pneumatic system - filter element |
Check the condition of the power supply |
|
Pneumatic system - filter element |
Check the condition of the main drive/motor shaft |
|
Pneumatic system - filter element |
Check the condition of the measuring system/barrier air |
|
Pneumatic system - filter element |
Check the condition of other filter elements |
|
Hydraulics |
Check the liquid level |
|
Hydraulics |
Check the accumulator |
|
Hydraulics |
Check the system pressure debugging status of the hydraulic device |
|
Cooling units and ventilators |
Check the liquid level |
|
Cooling units and ventilators |
Check the temperature adjustment according to the manufacturer's regulations |
|
Cooling units and ventilators |
Check the mixing ratio according to the manufacturer's regulations |
|
Cooling units and ventilators |
Check the condition of the filter screen |
|
Cooling units and ventilators |
Check the cooling medium (type) according to the regulations of the manufacturer |
|
Centralized lubrication |
Check the function of lubrication parts (sealing, grease overflow) |
|
Centralized lubrication |
Check the lubrication of the guide rail |
|
Centralized lubrication |
Check the condition of the lubricating medium |
|
Centralized lubrication |
Check the liquid level |
|
Centralized lubrication |
Check the liquid level. Inspection of lubrication media in accordance with manufacturing plant regulations |
|
|
|
|
Rail guard |
Check the scale board/slide board. |
|
Rail guard |
Check the liquid scraper. |
|
Shaft drive (ball screw drive/linear drive/circular shaft drive). |
Visual inspection |
|
Shaft drive (ball screw drive/linear drive/circular shaft drive). |
Detecting Noise |
|
Shaft drive (ball screw drive/linear drive/circular shaft drive). |
Detect vibration |
|
Main transmission device (motor shaft/ISM inductive electrostatic measuring device). |
Check traction and alternative dimensions. |
|
Main transmission device (motor shaft/ISM inductive electrostatic measuring device). |
Check the radial vibration pendulum of the spindle cone (300 mm in front of the spindle bulge site). |
|
Main transmission device (motor shaft/ISM inductive electrostatic measuring device). |
Check the spindle cone visually. |
|
Main transmission device (motor shaft/ISM inductive electrostatic measuring device). |
Visually inspect the slotted stone. |
|
Main transmission device (motor shaft/ISM inductive electrostatic measuring device). |
Check the function of the oil/lubrication mist. |
|
Main transmission device (motor shaft/ISM inductive electrostatic measuring device). |
Check the function of blocking air. |
|
Main transmission device (motor shaft/ISM inductive electrostatic measuring device). |
Check the filter on the ventilator (only for air-cooled inductive electrostatic measuring devices) |
|
Check for leakage |
Check the response characteristics of leakage monitoring/total leakage. |
|
Check for leakage |
Check the total leakage. |
|
Tool changer |
Visual inspection, basic function. |
|
Tool changer |
Check the wear of the tool holder. |
|
Tool changer |
Check the sensor debugging status. |
|
![]() |
![]() |
![]() |
Tool Magazine |
Check the sensor debugging status. |
![]() |
Tool Magazine |
Check the condition of opening and closing machinery. |
![]() |
Tool Magazine |
Check the cutter marker. |
![]() |
Tool Magazine |
Check the barrel, clamp/knife holder. |
![]() |
Cooling lubricant device |
Check the contamination of the cooling lubricant tank. |
![]() |
Cooling lubricant device |
Check the pressure of the high-pressure pump. |
![]() |
Cooling lubricant device |
Check the level monitoring device. |
![]() |
Cooling lubricant device |
Check the rolling paper belt filter monitoring device. |
![]() |
Machine protective cover |
Visually inspect the glass windows. |
![]() |
Machine protective cover |
Check the function of the door switch. |
![]() |
Machine protective cover |
Check the function of the emergency stop button. |
![]() |
Electric control cabinet |
Check the sealing. |
![]() |
Electric control cabinet |
Check the function of the electric cabinet radiator/filter ventilator. |
![]() |
Electric control cabinet |
Check the ventilator and filter/external adjustable heater. |
![]() |
Electric control cabinet |
Check the condition of the filter screen. |
![]() |
Options |
Check the workpiece handling device. |
![]() |
Options |
Check the workpiece measuring device/measurement probe. |
![]() |
Options |
Check the tool measuring device. |
![]() |
![]() |
![]() |
![]() |
Options |
Check the oil mist/lubricant mist extraction device. |
![]() |
Indicator for inspection |
The indicator for inspection is reset. |
![]() |
4.12.2 Inspection scope 2
After 4000 hours of operation, perform this first inspection according to inspection scope 2.
- Repeat inspection according to inspection scope 2, and change inspection according to inspection scope 1.
- The interval for checking scope 2 is 4000 hours.
|
|
|
Pneumatic |
Check the pressure debugging according to the pneumatic system table |
|
Pneumatic |
Visually inspect the automatic water separator |
|
Pneumatic |
Check the basic condition of the hose and pipe |
|
Pneumatic system - filter element |
Check the condition of the power supply |
|
Pneumatic system - filter element |
Check the condition of the main drive/motor shaft |
|
Pneumatic system - filter element |
Check the condition of the measuring system/barrier air |
|
Pneumatic system - filter element |
Check the condition of other filter elements |
|
Hydraulics |
Check oil change interval |
|
Hydraulics |
Check the liquid level |
|
Hydraulics |
Check the accumulator |
|
Hydraulics |
Check the system pressure debugging status of the hydraulic device |
|
Hydraulics |
Check the basic condition of the hose and pipe |
|
Cooling units and ventilators |
Check the liquid level |
|
Cooling units and ventilators |
Check the temperature adjustment according to the manufacturer's regulations |
|
Cooling units and ventilators |
Check the mixing ratio according to the manufacturer's regulations |
|
Cooling units and ventilators |
Check the condition of the filter screen |
|
Cooling units and ventilators |
Check the cooling medium (type) according to the regulations of the manufacturer |
|
Cooling units and ventilators |
Check the time interval for cooling medium replacement |
|
Centralized lubrication |
Check whether the filling hole on the device is clean |
|
|
|
|
Centralized lubrication |
Check the condition of the filter element |
|
Centralized lubrication |
Check the condition of the lubricating medium |
|
Centralized lubrication |
Check the liquid level |
|
Centralized lubrication |
Check the liquid level and check the lubricating medium according to the manufacturer's regulations |
|
Centralized lubrication |
Check lubrication parameters according to requirements/regulations |
|
Rail guard |
Check cover plate for secondary part of linear motor |
|
Rail guard |
Check the liquid scraper |
|
Guideway |
Check the condition of the guide |
|
Guideway |
Check the condition of the oil hookup |
|
Belt |
Check the condition of the belt |
|
Main transmission device (motor shaft / ISM induction electrostatic measuring device) |
Check traction and alternative dimensions. |
|
Main transmission device (motor shaft / ISM induction electrostatic measuring device) |
Check the sealing condition of the tool clamping device (also check the sealing condition of the transfer pipe in HSK) |
|
Main transmission device (motor shaft / ISM induction electrostatic measuring device) |
Typically check the debugging status of the sensor |
|
Main transmission device (motor shaft / ISM induction electrostatic measuring device) |
Check the radial vibration pendulum of spindle cone (300 mm in front of spindle bulge site) |
|
Main transmission device (motor shaft / ISM inductive electrostatic measuring device |
Visually inspect the spindle tape |
|
Main transmission device (motor shaft / ISM induction electrostatic measuring device) |
Visual inspection of slotted stones |
|
Main transmission device (motor shaft / ISM induction electrostatic measuring device) |
Check the function of lubrication/lubricating mist |
|
Main transmission device (motor shaft / ISM induction electrostatic measuring device) |
Check the function of blocking air |
|
Main transmission device (motor shaft / ISM induction electrostatic measuring device) |
Check the filter on the ventilator (only for air-cooled inductive electrostatic measuring devices) |
|
|
|
|
Check for leakage |
Check the replacement interval of the swivel joint |
|
Cooling lubricant device |
Check the contamination status of the cooling lubricant box |
|
Chip conveyor (Chip export device) |
Check the suction performance of the oil return pump |
|
Chip conveyor (Chip export device) |
Visual inspection of the drive chain |
|
Machine protective cover |
Visually inspect the glass window |
|
Machine protective cover |
Check the function of the door switch |
|
Machine protective cover |
Check the function of the emergency stop button |
|
Machine protective cover |
Are there safety prompts and alerts? Are they clearly readable? |
|
Electric control cabinet |
Check sealing condition |
|
Electric control cabinet |
Check the function of electric cabinet radiator/filter ventilator |
|
Electric control cabinet |
Check ventilators and filters/external adjustable heaters |
|
Electric control cabinet |
Check the condition of the filter screen |
|
Options |
Check the workpiece handling device |
|
Options |
Check the workpiece measuring device / measuring probe |
|
Options |
Check tool measuring device |
|
Options |
Check the oil mist and lubricant fog extraction device |
|
Indicator for inspection |
Reset indicator for inspection |
|
4.13 Maintenance
This profile is not available for procedural technical reasons.
4.14 Description of maintenance and repair
In this section, maintenance and repair are described, which can only be carried out by persons with qualifying grades 1 to 3.
The work of qualification level 4 is described in our company. Repair Service Manual, which will be issued when carrying out the maintenance service training in our company.
Qualification Level 5 requires the assistance of the Outsourcing Module Manufacturing Plant (see Outsourcing Module Manufacturing Materials).
Reminder!
A summary of what maintenance and repair work can be performed at what qualification level is not yet available for procedural technical reasons.
Soall of the following maintenance and repair can only be done by the machine owner.
4.14.1 Exterior of the machine
4.14.1.1 Overview of maintenance operations
- Clean the outside of the machine.
Cleaning the outside of the machine
Cleaning with compressed air is strictly prohibited.
Do not use compressed air when cleaning workpieces and machine tools.
The flying chips are dangerous mainly to human eyes!
Prerequisite
- The program is over.
- The machine is in a stop state.
Required Tools/Materials
- Clean rags should be soft and clean.
- Common neutral cleaners on the market without decontamination or strong alkaline additives.
Process
- Clean the surface of the protective cover.
- Machine tools have been cleaned from outside.
4.14.2 Interior of the machine
4.14.2.1 Overview of maintenance work
- Clean the inside of the machine.
- Clean the inside of the machine
Cleaning the outside of the machine
Do not use compressed air to clean the workpiece and machine tool.
The chips that fly by blowing will be at risk of personal injury, especially to the eyes.
Chips build up in the corners of the processing area.
Prerequisite
- The program is over.
- The machine is in a stop state.
Required Tools/Materials
- Hand broom
- Clean rags should be soft and clean.
- Rinse spray gun (according to machine configuration).
Process
- Clean the machine from the inside.
- Machine tools have been cleaned from inside.
4.14.3 Axis
4.14.3.1 X-axis
Overview of maintenance work
- Clean the corrugated box
- Clean the rails and oil.
- Check if the scraping device is damaged.
- Clean the scraping device
Automatic operation of machine tools.
Unforeseen dangerous effects due to sudden automatic activation during maintenance operations!
During all maintenance work, turn off the power cut-off device and prevent it from being turned on with a padlock.
Clean the corrugated box
Prerequisite
- The power partition unit is off and locked with a padlock.
- The X-axis is in the end position.
Required Tools/Materials
- Hand broom
- Industrial vacuum cleaners
Process
- Corrugated box pumping.
- Clean the corrugated box.
- The corrugated box has been cleaned.
Clean the guide and apply oil
Prerequisite
- The power partition unit is off and locked with a padlock.
- The X-axis is in the end position.
- Required Tools/Materials
- Industrial vacuum cleaners
- Cleaning with a cloth
- Ordinary rust oil.
Process
- Loosen the fixing bolts of the right corrugated box
- Move the bellows box to the right.
- Clean exposed areas of the X-axis guide and grease them.
- Clean the exposed area of the ball screw and apply oil.
- Move bellows to the left and retighten retaining bolts.
- Simulate the execution of the process on the left side of the workbench.
- The rails have been cleaned and oiled.
Check the scraping device for damage and clean it.
Prerequisite
The power partition unit is off and locked with a padlock.
Move the bellows back.
Required Tools/Materials
- Cleaning with a cloth
- Ordinary rust oil.
Process
- Check the scraping device on the guide vehicle for damage.
- Scratch device is not damaged: end maintenance work.
- Scratch device has been damaged: ask our company technical service department to replace the scraping device.
- Clean the scrapping device on the guide car.
- Check the scattering device on the scale for damage.
- Scratch device is not damaged: end maintenance work.
- Scratch device has been damaged: ask our company technical service department to replace the scraping device.
- Check the scraping device of the scale and apply oil.
- Scratch device has been checked and oiled.
4.14.3.2 Y-axis
Overview of maintenance work
- Cleaning workspace guard
- Clean the rails and oil.
- Check if the scraping device is damaged.
- Clean the scrapigdevice
Automatic operation of machine tools.
Unforeseen dangerous effects due to sudden automatic activation during maintenance operations!
During all maintenance work, turn off the power cut-off device and prevent it from being turned on with a padlock.
Cleaning workspace guard
Prerequisite
- The power partition unit is off and locked with a padlock.
- Y-axis is in the end position
Required Tools/Materials
- Hand broom
- Industrial vacuum cleaners
Process
- Open the machining area door.
- Work area guard and Y-axis exposed area pumping wind.
- Clean the workspace guard and the Y-axis exposed area.
- The workspace guard and Y-axis dew area are cleaned.
Clean the rails and apply oil
Prerequisite
- The power partition unit is off and locked with a padlock.
- Y-axis is in the end position
Required Tools/Materials
- Industrial vacuum cleaners
- Cleaning with a cloth
- Ordinary rust oil.
Process
- Open the machining area door.
- Clean the exposed area of the Y-axis guide rail and apply oil.
- Close the door to the processing area.
- Remove the right side of the machine maintenance cover.
- Clean the exposed area of the Y-axis guide rail and apply oil.
- Clean the exposed area of the ball screw and apply oil.
- Install the maintenance guard.
- The rails have been cleaned and oiled.
Check the scraping device for damage and clean
Prerequisite
- The power partition unit is off and locked with a padlock.
Required Tools/Materials
- Cleaning with a cloth
- Ordinary rust oil.
Process
- Open the machining area door.
- Check the scraping device on the guide vehicle for damage.
- Scraping device is not damaged: end maintenance work.
- Scraping device has been damaged: Replace it with the scrapping device from our company.
- Clean the scrapping device on the guide car.
- Close the door to the processing area.
- Similar to the work flow above the maintenance guard on the right side of the workbench.
- Scratch device has been checked and oiled.
4.14.3.3 Z-axis
Overview of maintenance work
- Cleaning workspace guard
- Clean the rails and oil.
- Check if the scraping device is damaged.
- Clean the scrapingdevice
Automatic operation of machine tools.
Unforeseen dangerous effects due to sudden automatic activation during maintenance operations!
During all maintenance work, turn off the power cut-off device and prevent it from being turned on with a padlock.
When the safety device fails, the Z axis descends.
A personal risk that may result in death or serious bodily injury.
- The Z-axis supports or runs to a safe position.
- Never stop below the Z-axis.
Cleaning workspace guard
Prerequisite
- The power partition unit is off and locked with a padlock.
- The Z-axis is in the terminal position.
Required Tools/Materials
- Hand broom
- Industrial vacuum cleaners
Process
- Open the machining area door.
- Extraction of air from the work area guard and the exposed area of the Z-axis.
- Clean the workspace guard and Z-axis exposed area.
- Close the door to the processing area.
- The workspace guard and Z-axis exposed areas are cleaned.
Clean the guide and apply oil
Prerequisite
The power partition unit is off and locked with a padlock.
- The Z-axis is in the terminal position.
- Required Tools/Materials
- Industrial vacuum cleaners
- Cleaning with a cloth
- Ordinary rust oil.
- Conductor
Process
- Open the machining area door.
- Clean the exposed area of the Z-axis guide rail and apply oil.
- Use a ladder to clean and oil the upper part of the Z-rail.
- Close the door to the processing area.
- The rails have been cleaned and oiled.
Check the scraping device for damage and clean
Prerequisite
- The power partition unit is off and locked with a padlock.
- Required Tools/Materials
- Cleaning with a cloth
- Ordinary rust oil.
Process
- Open the machining area door.
- Check the scraping device on the guide vehicle for dam
- Scratch device is not damaged: end maintenance work.
- Scratch device has been damaged: ask our company technical service department to replace the scraping device.
- Clean the scrapping device on the guide car.
- Close the door to the processing area.
- Scratch device has been checked and oiled.
4.14.4 Viewing Glass
4.14.4.1 Overview of maintenance work
- Clean the viewing glass.
- Check whether the window glass is damaged.
- Determine the impact blocking capacity of the sight glass.
Machine tools run automatically!
Unforeseen dangerous effects due to sudden automatic activation during maintenance operations!
During all maintenance work, turn off the power cut-off device and prevent it from being turned on with a padlock.
Clean the viewing glass of the machine
Example display of all window glass for machine tools.
Polycarbonate window glass for machining door! There is a danger of deformation and corrosion.
Only the right liquid is allowed to clean the door window glass in the processing room.
Prerequisite
- The power partition unit is off and locked with a padlock.
Required Tools/Materials
- Clean rags should be soft and clean.
- Use common neutral or glass cleaners on the market, without decontamination or strong alkaline additives.
Process
- Observe glass from the external and internal cleaning machine tools (including unshown parts).
- End maintenance work. Check the door of the processing area to see if glass is damaged
Damage is present in the following cases,
- When the inner and outer glass has cracks or the frame seal is torn, damaged or its surface is severely scratched
- When plastic deformation occurs when subjected to impact load.
Polycarbonate window glass for machining door!
In damaged viewing glass, there is a risk of high energy penetration by an unsecured workpiece or a broken tool tip!
- When the window glass is damaged or plastically deformed, the machine should be stopped immediately and the window glass should be replaced by the after-sales service personnel of our company.
- Machine tools with damaged viewing glass are strictly prohibited!
- Please record the date when replacing the viewing glass.
Prerequisite
- The power partition unit is off and locked with a padlock.
Required Tools/Materials
- Spare parts: the processing shop window glass
Process
- Visually check the inside and outside sides of the door window glass (1) in the processing room for damage and plastic deformation.
- Processing room door window glass undamaged: end maintenance work.
- Window glass damage in the processing room: Machine tools immediately shut down, and replace the processing area door viewing glass through our company after-sales service department.
- Repair and maintenance finished
Determine the ability of machining door window glass to block impact
The viewing glass in the processing area that is not damaged on the outside bears the following loads:
- cooling lubricant
- cleansers
- tallow
- oils
- other corrosive media
The aging process will lead to quenching. Therefore, the viewing glass in the processing area is classified as a consumable part. The ability to block impact of window glass in the processing room depends on
- the diameter of tool used.
- speed used.
- aging degree of glass.
The replacement is done through the after-sales service department of our company.
According to the characteristic curve, the blocking performance is determined
As seen in the characteristic curve chart, the maximum allowable tool diameter and maximum permissible speed of an observation glass without damage depends on its aging degree. According to the German Standard DIN EN 12417 there is a potential risk when flying out parts with a mass of 100 g.
The curve chart is suitable for cooling lubricants or other corrosive media.
The service life will be extended by 2 years without taking into account the effect of cooling lubricants or other corrosive media.
The allowed tool speeds follow the instructions of the tool manufacturer, and not according to the theoretical limits in the characteristic curve chart.
Tool and speed allowed for 12 mm polycarbonate glass.
1. 4 years old 2. 6 years old 3. 8 years old
4.Maximum spindle speed [1/min] 5. Maximum tool diameter [mm]
For example: when viewing glass is used for 6 years, the theoretical permissible speed of a 150 mm diameter tool is 10000 1/min.
4.14.5 Operating console
4.14.5.1 Overview of maintenance operations
- Clean the console.
4.14.5.2 Cleaning operating console
Compressed air cleanup is strictly disabled
Compressed air should not be used to clean the operating console.
Prerequisite
- The program is over.
- The machine has been stationary.
Tools/Materials required
- Clean rags should be soft and clean.
- Common neutral cleaners on the market, without contamination or strong alkaline additives.
Process
- Clean the operating table from outside.
- The operating console has been cleaned.
4.14.6 Emergency stop button
4.14.6.1 Overview of maintenance operations
- Functional Check
Functional Check
Check each emergency stop button located on the machine.
If the drive is not shut down, stop immediately and notify the after-sales service department of our company!
Prerequisite
- The program is over.
- The machine has been stationary.
- The drive has been switched on.
- Runtime
- Press the emergency stop button.
All movement will be stopped.
The immediate stop of the sliding table and spindle may cause damage to the machine tool.
Press the emergency stop button at dangerous times.
The drive will be shut down,
The emergency stop button function has been checked.
4.14.7 Manual of inside operation
4.14.7.1 Overview of maintenance operations
- Function check for emergency unlocking from outside
- Function check for emergency unlocking from outside
Prerequisite
- The processing room door is locked.
Required Tools/Materials
- Screwdrivers
Process
- Unscrew the locking bolt (2).
- Use a change cone to turn the unlock disc (3) around 90° along the arrow direction.
- The processing room is unlocked.
- Reset the emergency unlock.
- Checked for the function that was unlocked from the internal emergency.
4.14.8 Door of the processing room
4.14.8.1 Overview of repair work
- Clean the guide rails and apply oil.
Automatic operation of machine tools.
Unforeseen dangerous effects due to sudden automatic activation during maintenance operations!
- During all maintenance operations, turn off the power cut-off device and lock it with a padlock to prevent accidental connection.
Clean the rails and apply oil
Prerequisite
- The power cut-off device has been switched off and locked with a padlock.
- The processing room door has been opened.
Required Tools/Materials
- Cleaning with a cloth
- Ordinary rust oil.
Process
- Clean the guide rails and apply oil.
- The rails have been cleaned and oiled.
4.14.9 Electric control cabinets
4.14.9.1 Overview of maintenance work
- Check the joints and connections inside the electric control cabinet.
Check the joints and connections inside the electric control cabinet.
Prerequisite
- The power cord is disconnected and locked to make sure it is not turned on.
Required Tools/Materials
- Torch
- Installation tools
Process
- Open the electric control cabinet
Warning! Dangerous voltage!
There is also a high voltage when the power-separation device is turned off. An electric shock can cause death or serious injury.
- Disconnect the power supply and lock it to make sure it is not connected.
- Only allow electricians to work in the electric control cabinet
- Check that the joints and connections are secure.
- If necessary, tighten the joints and connections.
- Turn off the electric control cabinet.
- The internal joints and connections of the electric control cabinet have been checked.
4.14.10 Host buffer batteries
4.14.10.1 Overview
This machine CNC system is equipped with a backup battery. The backup battery is responsible for powering the machine CNC system main computer after shutdown. This prevents RAM-memory data loss.
When the buffer battery is removed, an alarm information divided into three levels will be displayed on the controller display.
Diagnostic instructions for the plant. When the first level is displayed, the buffer battery must be replaced within 6 weeks because there is only a limited remaining power.
If this alarm information is ignored and the buffer battery is not replaced by the specified deadline, there may be a string or loss of program and machine data.
It is recommended to back up the data to an external data carrier or PC before replacing the battery.
4.14.10.2 Overview of maintenance operations
Warning! Dangerous voltage! High voltage.
There is a risk of electrocuting life.
- Cut off the power cord voltage and padlock to prevent unintentional indirect pass.
- Only those with training are allowed to replace backups batteries.
- Replace the backup battery
4.14.10.3.Replacement of the backup battery
1. Dual fan-/battery-module 2. Backup battery
3. Pressure point 4. Main computer (PCU)
To save RAM-memory data, a buffer condenser is used. Without the buffer condenser, the capacitor retains the data in RAM-memory for approximately 30 minutes.
Prerequisite
- Turn the machine power off on the power disconnect unit and lock the power disconnect device with a padlock.
- Cut off the power cord voltage and padlock to prevent unintentional indirect pass.
- Required Tools/Materials
- Spare parts: backup battery.
Process
Open the electric control cabinet.
Don't rough pull out dual ventilator modules/battery-modules.
Dual Ventilator Module/Battery - The hook on the module may be removed and the dual ventilator modules/battery-modules can no longer be inserted.
- Dual Ventilator Module/Battery-Module can only be pulled out when the lock unit is fully loosened.
- Loosen the locking device of the double ventilator module/battery-module (1) on the pressure point (3) and carefully disconnect the double ventilator module/battery-module from the main computer (4).
- Replace the backup battery (2).
- Dual Ventilator Module/Battery - The module replugged on the main computer and meshed well.
- Turn off the electric control
- This backup battery has been replaced.
4.14.11 Electric control cabinet cooling station
4.14.11.1 Overview of maintenance work
- Clean the blinds.
- Check condensate drainage.
- Replace the filter pad.
Automatic operation of the cooling station!
Unforeseen dangerous effects due to sudden automatic activation during maintenance operations!
- During all maintenance work, turn off the power cut-off device and prevent it from being turned on with a padlock.
Clean blinds
1 blinds grille
Incompletely cleaned louver grilles may seriously affect the ventilation of the airflow, and may cause the consequences of the failure of the cooling station, and even the shutdown of the machine tool.
Prerequisite
- The power partition unit is off and locked with a padlock.
- Required Tools/Materials
- Under normal ambient air conditions: common neutral cleaners on the market
- Under oily ambient air conditions: solvents that dissolve oil, such as cleaning gasoline
- Clean sea cotton
- Compressed air or dry rag
Process
- Pull down the shutter grille (1) and clean it.
- Dry the 100-page grille and insert it again on.
- The blinds have been cleaned.
Checking condensate drainage
1 Condensate discharge port
Secure a section of the hose to the discharge outlet of the condensate so that the dripping condensate residue cannot be retained in the cooling station.
Prerequisite
- The power partition unit is off and locked with a padlock.
Process
- Visually inspect the condensate drain (1) for blockage and smooth
- Condensate discharge smoothly: end maintenance work.
- Unnormal discharge of condensate: troubleshooting.
- Condensate discharge has been checked.
Replace the filter pad
- Failure to replace or replace the filter mat too late will seriously affect the air flow, and cause the failure of the cooling station and the downtime of the machine tool.
- The status of the filter pad will be monitored. When an error notification appears on the display of the numerical control system, the filter mat must be replaced immediately.
- Visually inspect the filter pad when no error notification is displayed. When it is visibly dirty: replace the filter pad preventively in advance.
When the air contains excessive oil mist, a metal filter can be used for multiple applications. The metal filter can be cleaned with a solvent that dissolves oil, such as cleaning gasoline.
Prerequisite
- The power partition unit is off and locked with a padlock.
Required Tools/Materials
- Spare parts: filter pad
Process
- Pull down the shutter grille.
- Remove the filter pad.
- Insert new filter pad.
- Log the blinds grille again.
- The filter pad has been replaced.
4.14.12 Tool magazine body chain
Added amount [l] |
Greases |
Positions |
Even on the roller |
Turmogrease L252/3 Multipurpose Grease |
Tool magazine chain |
4.14.12.1 Overview of maintenance work
- Check the liquid level.
- Supplement with the addition of lubricant.
4.14.13 Working spindle
4.14.13.1 Spindle taper hole SK/CAT/BT
Added amount [l] |
Lubricants |
Liquid level |
Remark |
- |
MOLYKOTE-Spray |
- |
- |
Overview of maintenance work
Automatic operation of machine tools.
Unforeseen hazardous effects due to sudden automatic start during maintenance operations.
- During all maintenance operations, turn off the power cut-off device and lock it with a padlock to prevent accidental connection.
- Clean the spindle taper hole.
- Spray cleaner on spindle cone hole.
- Check spindle taper hole for damage.
- Clean spindle cone hole
1 spindle taper hole
Prerequisite
- The power cut-off device has been switched off and locked with a padlock to prevent it from being switched on.
Required Tools/Materials
- Leather cleaning rags
Work flow
- Clean the spindle tapered bore (1) annularly.
- The spindle cone hole has been cleaned.
Spindle cone spray cleaner
1 spindle taper hole
Prerequisite
- The power cut-off device has been switched off and locked with a padlock to prevent it from being switched on.
Required Tools/Materials
- MOLYKOTE-Spray
Process
- Spray the cleaning agent along the ring on the spindle taper hole (1).
- Cleaner has been sprayed on the spindle cone hole.
Inspect spindle taper hole for damage
1 spindle taper hole
Prerequisite
- The power cut-off device has been switched off and locked with a padlock to prevent it from being switched on.
Required tools/Materials
- Torch
Process
- Inspect the spindle tapered bore (1) for recognizable damage.
- The spindle taper hole has been checked.
- If the spindle cone hole is damaged: entrust our companyafter-sales department to replace the damaged parts.
4.14.14 Hoses and pipes
4.14.14.1 Overview of maintenance work
- Visual inspection of sealing.
- Replace the hydraulic line.
Visual inspection of sealability
Prerequisite
- The power partition unit is off and locked with a padlock.
Required Tools/Materials
- Cleaning with a cloth
- Torch
Process
- Turn on the media supply.
Caution! Hot hot surface! Heat heating pumping station.
Risk of injury from scalding due to contact.
- Please cool down the pump station before all maintenance work.
Check the tightness of hoses and pipes.
Hose and plumbing abnormal: machine shutdown and replacement of damaged pieces.
The tightness has been inspected visually. Replace the hydraulic line.
Replacement of hydraulic lines must be made by qualified maintenance personnel.
4.14.15 Hydraulic pumping station
Added amount [l] |
Lubricants |
Liquid level |
Remark |
1.9 |
Hydraulic oil HLP/HLP-D 46 |
Highest - Minimum level mark according to glass window |
If the oil level drops below the highest to half of the lowest oil level mark, fill up the oil. |
To ensure smooth operation of the unit, hydraulic fluid must be replaced during a specified maintenance cycle.
- Maintenance period description “According to specific conditions” is 4,000 hours at the time of this task, or the maintenance task is performed once a year.
4.14.15.1 Overview of maintenance work
- Check the liquid level
- Check the contamination level of the filter
- Replace oil
Caution! Hot surface!
There is a danger of scalding when the heated hydraulic pump station comes into contact with the hydraulic oil.
- Allow the hydraulic pump station to cool down before performing all maintenance work.
Automatic operation of hydraulic pump station.
Sudden automatic operation during maintenance operations will have unforeseen dangerous consequences.
- Switch the main switch off and lock with a padlock to prevent accidental connections during all maintenance jobs.
Check the liquid level
1 plus injection 2 level meter
Supplement only the same brand of hydraulic oil. Do not mix oils from different manufacturers or varieties.
Prerequisite
- The main switch is turned off and locked with a padlock.
Required Tools/Materials
- Hydraulic Fluid HLP / HLP-D 46
- Fueling funnel
Process
- Check the level on the level indicator (2).
- The liquid level is in the upper half of the highest and lowest marks: end maintenance.
- The liquid level is in the lower half of the highest and lowest marks: refuel.
Supplemental refueling
To ensure that the hydraulic system operates reliably, only add fresh filtered hydraulic oil.
Refuel the pumping station through an absolute fine filter 20 µm or filter unit.
- Remove the filling bolt.
- Refill oil through the oil filling port (1) to reach the highest level mark.
- Pack the injection bolt again.
- Refueling has been completed.
Oil change
1 Filling hole 2 Level gauge 3 Pressure discharge bolt
To ensure that the hydraulic system operates reliably, only add fresh filtered hydraulic oil.
Prerequisite
- The main switch is turned off and locked with a padlock.
- Pressure in hydraulic pumping stations and pipes has been unloaded.
Required Tools/Materials
- Hydraulic Fluid HLP / HLP-D 46
- Collecting box
- Fueling funnel
- Installation tools
Process
Hydraulic pump stations and pipelines under pressure.
The hydraulic oil sprayed under high pressure can cause injury.
Before changing the oil, make the hydraulic pump station pressure-free.
- Eliminates pressure by slowly levol pressure unloading bolts (4).
- When no pressure is displayed, the oil can be changed.
- Open the gas port in order to exhaust (1).
- Unscrew the drain bolt (3) to completely drain the oil into the oil container.
- Reinstall the discharge bolt (3).
- Fill oil through the oil filling hole (1) until the maximum oil level mark of the oil level indicator (2) is reached.
- Please close the gas port (1).
- Turn the pressure relief screw (3) to the right until it is blocked.
- The pressure will build again.
- Turn on the power of the machine tool at the main switch and turn on the drive at the CNC system console.
- The pressure of the hydraulic pump station will automatically build up.
- Check the level on the level indicator (1).
- The liquid level is below the highest mark: add oil, see the section "Checking the liquid level".
- The level is located at the highest mark: end maintenance
4.14.15.2 Checking nitrogen pressure
1 Pressure discharge bolt 2 Pressure gauge 3 Cover
Prerequisite
- The main switch is turned off and locked with a padlock.
Required tools/Materials
- Pressure gauge
Process
- Unload the system pressure at the pressure discharge bolt (1).
- Unscrew the protective cover (3) of the measuring interface.
- Connect the pressure gauge (2) to the measuring interface of the accumulator.
- Turn off the pressure unloading bolt (1).
- Turn the main switch of the control cabinet to the "I" position.
- Press the “On” key.
- System pressure will be established.
- Press the emergency stop button.
- Slowly open the pressure relief bolt (1) and observe the system pressure on the pressure gauge (2).
- A slow and uniform pressure drop will be displayed.
- Only after the hydraulic accumulator is completely empty, its pressure drops sharply.
- The overpressure read before the pressure drop corresponds to the pre-fill pressure of the hydraulic accumulator.
- The nitrogen pressure has been checked.
4.14.16 Pneumatic units
1 Compressed air line 2 Pressure gauge 3 Pre-filter 4 Drain valve
4.14.16.1 Overview of maintenance work
- Check the pressure on the pressure gauge.
- Emissions of condensate.
- Replace the pre-filter.
- Clean the filter tank.
Automatic operation of machine tools.
Sudden automatic operation during maintenance operations will have unforeseen dangerous consequences.
During all maintenance work, turn off the power cut-off device and prevent it from being turned on with a padlock.
The following items must be paid attention to during maintenance operations:
- If required, depressurize the pneumatic maintenance unit.
- The pressure pointer on the pressure gauge (1) must point to "0".
- When there is only pressure, unload the pressure by turning left on the pressure regulator (3).
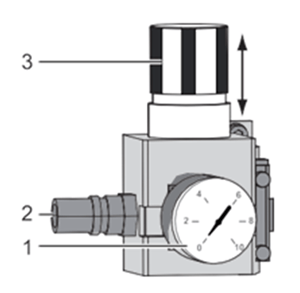
1 Pressure gauge 2 Compressed air line 3 Pressure regulator
Prerequisite
- The compressed air pipeline has been connected.
Work flow
-
- Pull the pressure regulator (3) upwards.
- Check the pressure of the pressure gauge (1) at 6.5-8.0 bar and adjust it on the pressure regulator (3) if necessary.
- Turn the pressure regulator to the right (pressure drop increases).
- Turn the pressure regulator to the left (pressure drops).
- Push down the knob of the pressure regulator.
- The pressure on the pressure gauge has been checked.
- Emissions of condensate.
1 Compressed air line 2 Drain valve
Prerequisite
- The power partition unit is off and uses a padlock to prevent it from being connected.
- The compressed air system is no longer under pressure.
Work flow
- Drain the condensate by pressing the drain valve (2).
- Install compressed air line(1) again.
- Replace coarse filter
1 Compressed air line 2 Pre-filter 3 Buffer disk 4 O-ring 5 Filter tank
Clean the filter tank when replacing the filter.
Prerequisite
- The power partition unit is off and uses a padlock to prevent it from being connected.
- The compressed air system is no longer under pressure.
Required Tools/Materials
- Spare parts: pre-filter
Work flow
- Turn left and unscrew filter tank (5).
- Hold the prefilter (2) and unscrew the buffer tray (3).
- Remove the old prefilter.
- Insert a new coarse filter and fix the impact disk.
- Coating grease on the O-ring (4).
- Screw on the strainer tank.
- Install the compressed air line (1) again.
- The coarse filter has been replaced.
Cleaning the filter tank
1 Compressed air line 2 O-ring 3Filter tank
Prerequisite
- The power partition unit is off and uses a padlock to prevent it from being connected.
- The compressed air system is no longer under pressure.
Required Tools/Materials
- Wash pots
- Water, kerosene, cleaning gasoline
- Lubricating grease
Process
- Turn left and unscrew filter tank (3).
Filter tank made of polycarbonate material! There is a danger of deformation and corrosion.
Clean the filter tank only with a suitable liquid.
- Clean the filter tank.
- Coating grease on the O-ring (2).
- Screw on the strainer tank.
- Install the compressed air line (1) again.
- The filter tank is clean and clean.
14.4.17 Central lubrication
Added amount [l] |
Lubricants |
Liquid level |
Remark |
1.8 |
Thin grease GP 000 K-20 |
According to the highest-lowest level mark of oil tank |
When the liquid level drops to the lower half of the highest-lowest liquid level mark, add it. |
4.14.17.1 Overview of maintenance work
- Check the liquid level.
- Supplemental addition of diluted grease.
Automatic operation of central lubrication
Unforeseen dangerous effects due to sudden automatic activation during maintenance operations!
During all maintenance work, turn off the power cut-off device and prevent it from being turned on with a padlock.
Check the liquid level
1 Filling hole 2 max level 3 minimum level
If the fault message "below the axis lubricating oil level" appears on the display of the numerical control system, liquid grease must be added immediately, otherwise the automatic operation (cycle start) will be prohibited after the reaction time has passed.
Prerequisite
- The power partition unit is off and locked with a padlock.
Required Tools/Materials
- dilute grease
Process
- Check the liquid level on the level indicator of the central lubrication unit.
- The level is in the bottom half of the highest, lowest mark: add dilute grease.
- The liquid level is in the upper half of the highest and lowest marks: end maintenance. Replenishment adddilute grease
Prerequisite
- The power partition unit is off and locked with a padlock.
Required tools/Materials
- fueling funnel
- dilute grease
Process
- Remove the cap from the filler port.
- Replenish dilute grease to the highest level.
- Closes the lid of the notch.
- Fluid grease replenished
4.14.18 Processing spindle lubrication station
Added amount [l] |
Lubricants |
Liquid level |
Remark |
1,8 |
Lubricant CLP 68 |
According to the highest-lowest level mark of oil tank |
When the liquid level drops to the lower half of the highest-lowest liquid level mark, add it. |
4.14.18.1 Overview of maintenance work
- Check the liquid level.
- Supplement with the addition of lubricant.
- Check the pressure on the pressure gauge.
- Inspect and replace filter cores as necessary.
Automatic operation of lubrication pump station!
Unforeseen dangerous effects due to sudden automatic activation during maintenance operations!
During all maintenance work, turn off the power cut-off device and prevent it from being turned on with a padlock.
Check the liquid level
1 plus injection hole 2 max level 3 minimum level
Prerequisite
- The power partition unit is off and locked with a padlock.
Process
- Check the liquid level on the liquid level indicator of the lubrication pump station.
- The liquid level is in the upper half of the mark between the highest and the lowest liquid level: end the maintenance work.
- Level at highest - lower half of the lowest level mark: add dilute grease.
As long as there is a failure notification on the screen of the CNC system, you must add lubricating oil, otherwise, the automatic operation will be prohibited after the reaction time (cycle start).
Supplemental addition of lubricant.
To ensure the equipment is running smoothly, refill only new filtered lubricants.
Filters must be loaded at the lubrication pump station refueling range.
Prerequisite
- The power partition unit is off and locked with a padlock.
Required Tools/Materials
- Hoppers
- Lubricant CLP 68
Work flow
- Remove the cap from the filler port.
- Supplemental addition of lubricant to the highest oil level.
- Closes the lid of the notch.
- Supplemental addition of lubricant finished.
Check pressure on pressure gauge
1 Pressure Regulator 2 Pressure Gables
Prerequisite
- The pressure hose connected to the pressure gauge.
Process
- Pull the pressure regulator (1) up and out.
- Check the pressure on the pressure gauge (2) to reach 0.5 bar. If necessary, readjust on the pressure regulator (1).
- Turn the knob of the pressure regulator to the right (the pressure will increase).
- Turn the knob of the pressure regulator to the left (the pressure will decrease).
- Press down the regulator (1).
- The pressure of the pressure gauge has been checked.
Replace the filter cartridge
1 pollution level indication 2 tank 3 O-ring 4 filter tank 5 filter core
Clean the filter tank when replacing the filter.
Prerequisite
- The power partition unit is off and locked with a padlock.
- The compressed air system is no longer under pressure.
Required Tools/Materials
- Spare parts: Filter cartridge, O-ring
Process
- The compressed air line has been removed.
- Turn left and unscrew filter tank (4).
- Remove the filter cartridge (5).
- Insert the new filter element into the tank (2).
- Check the O-ring (3) for damage and replace it if necessary.
- Screw on the filter can (4).
- The filter cartridge has been replaced.
4.14.19 Machine tool heat exchangers
Added amount [l] |
Lubricants |
Liquid level |
Remark |
Up to 7,5 At least 5,5 |
Coolant consists of the following: • 30% Glysantin [G48 Protect Plus] • 70% softened water |
Marked according to highest and lowest coolant levels |
When the liquid level drops to the lower half of the mark between the highest and the lowest liquid level, refill. |
Check and maintain the chemical characteristics of the coolant according to the regulations on the ethylene glycol G48 data sheet.
In order to ensure the smooth operation of the device, the coolant must be replaced during the prescribed maintenance period.
Maintenance period description “According to specific conditions” is 4,000 hours at the time of this task, or the maintenance task is performed once a year.
4.14.19.1 Overview of maintenance work
Caution! Hot surface!
Heated cooling units and pipes. Scalding danger at contact.
Before each maintenance work, the surface of the cooling station should be radiated and cooled.
Automatic operation of the cooling unit.
Unforeseen hazardous effects due to sudden automatic start during maintenance operations.
Turns the power partition off while maintaining a job and stopping it from connecting with a padlock.
- Check the liquid level.
- Supplemental addition of coolant.
- Clean the filter grille.
- Clean the cooler blades.
Check the liquid level
1 highest level display 2 lowest level display
Prerequisite
- The power partition unit is off and locked with a padlock.
Process
- Check the level on the level indication.
- If the liquid level is in the upper half of the mark between the highest and lowest liquid level: no action is required.
- If the liquid level is in the lower half of the mark between the highest and lowest liquid level: add more coolant.
- Liquid level checked.
Supplemental addition of coolant.
1 Injection Bolt
Pay attention to the correct composition ratio of the coolant mixture!
Prerequisite
- The power partition unit is off and locked with a padlock.
Required Tools/Materials
- fueling funnel
- coolant
Process
- Unscrew the filling bolt (1).
- Add coolant to the upper mark of the liquid level indicator. To complement the addition, use a funnel with a suitable filter!
- Screw on the fueling screw (1).
- Coolant has been added.
Clean filter grille
1 filter grid (metal)
Under the most unfavorable environmental conditions, we recommend checking the shutter grille every day and cleaning it once a week.
Unfavorable environmental conditions:
- Polluted air.
- Temperatures over 30°C.
- Heat buildup is caused by narrow intervals with walls, roofs, or other machines.
- Obstruction to air suction and air discharge.
Use only original spare parts or lose warranty liability.
Prerequisite
- The power partition unit is off and locked with a padlock.
Required Tools/Materials
- Common neutral cleaners on the market.
- Clean sea cotton
- Compressed air or dry rags.
Process
- Lift the filter grid (1) slightly and pull it out.
- Clean filter grille (1).
- Install the filter grid (1) again.
- The filter grid has been cleaned (1).
Clean Cooler Blades
1 Cooler sheet 2 Filter grid (metal)
When the environmental conditions are unfavorable, it is recommended to check the cooler blades (1) daily and clean them weekly.
Unfavorable environmental conditions:
- Polluted air.
- Temperatures over 30°C.
- Heat buildup is caused by narrow intervals with walls, roofs, or other machines.
- Obstruction to air suction and air discharge.
Use only original spare parts, or else lose warranty liability.
The cooler blades are very sensitive to external forces. There must be no bending or damage when cleaning the cooler blades.
Prerequisite
- The power partition unit is off and locked with a padlock.
Required Tools/Materials
- Industrial vacuum cleaners
Process
- Lift the filter grid (2) slightly and pull it out.
- Carefully clean the shutters of the cooler from inside out (1) with compressed air.
- Install the filter grid (2) again.
- Cleaned cooler blades.
4.14.20 Chip discharges
Added amount [l] |
Lubricants |
Liquid level |
Remark |
180 |
Cooling lubricant |
Depending on the level of the chip discharge. |
Add it when the liquid level in the cooling lubricant device drops to the lower half between the highest-lowest mark. |
4.14.20.1 Overview of maintenance work
- Check the liquid level and add it if necessary.
- Check and clean the screen basket.
- Clean chip conveyor.
- Replace the coolant lubricant.
- Check and readjust the tension of the conveyor belt if necessary.
Machine tools and chip conveyors run automatically!
Unforeseen dangerous effects due to sudden automatic activation during maintenance operations!
During all maintenance work, turn off the power cut-off device and prevent it from being turned on with a padlock.
Exception to add cooling lubricant.
Check the liquid level
1 Maximum Level 2 Minimum
Pay attention to the provisions in the section "Cooling lubricants" on precautions for application and maintenance of cooling lubricants.
When supplementing the cooling lubricant, the diluted cooling lubricant will be added because the concentration will increase through atomization.
Cooling lubricants in chip conveyor containers are used to cool circulation between lubricant units, machines and chip conveyors. Its level fluctuates between the highest level (1) and the lowest level (2). Read out the level of the coolant lubricant unit at rest.
Prerequisite
- The machine and drive are powered off.
- Checked for the status of emulsifier.
- The container has been checked for dirt and sludge accumulation.
Required Tools/Materials
- Cooling lubricant
Process
- Check the level of the cooling lubricant device at the level gauge.
- The liquid level is in the upper half of the highest and lowest marks: end maintenance.
- The liquid level is in the lower half of the highest and lowest marks: add cooling lubricant.
- Liquid level checked.
Supplemental addition of cooling lubricant
The addition of direct replenishment by the coolant lubricant device may lead to overflow, so this method is not recommended.
Process
- Diluted cooling lubricant has been added through the chip conveyor.
- Check the liquid level of the cooling lubricant device.
- Repeat the Process if necessary.
- Cooling lubricant has been supplemented.
Check and clean screen baskets
1 cover 2 screen basket
Wear protective glasses when cleaning with compressed air
Prerequisite
- The main switch is turned off and locked with a padlock.
Required Tools/Materials
- airbrush
Process
- Cut off the electrical connection and unplug the delivery hose.
- Remove cover (1)
Blockage of the nozzle in the clean liquid range with chips
Please note that no chips should enter the purification range when removing the filter basket
- Push the screen basket (2) out with a handle.
- Check screen basket and chip removal
- Clean the filter basket with compressed air
- Assemble in reverse order.
- Cleaned filter basket
- Cleaner Chip Discharges
Please pay attention to the precautions on the use and maintenance of cooling lubricants in the chapter on maintenance. Add system cleaner 24 hours before cleaning the chip conveyor.
Pay attention to the position of the O-ring when the pump is assembled.
Wear protective glasses when cleaning with compressed air
Prerequisite
- The main switch is turned off and locked with a padlock.
Required Tools/Materials
- Airbrush
- System Cleaner
- Suction device
- Cleaning accessories: cleaning rags, brushes.
- Water used for flushing.
Process
- Cut off the electrical connection and unplug the delivery hose.
- Remove coolant pump (4) and clean.
- Pump out the cooling lubricant.
- Pull the chip conveyor forward under the machine tool.
- Remove cover (1)
- Push the screen basket (2) out with a handle.
- Clear chips from the filter basket and clean the filter basket with compressed air
- Cleaned filter basket
- Thoroughly clean the cooling lubricant box (3) and the cavities of the chip conveyor
- Assemble in reverse order.
- Clean the shell of the chip conveyor.
- The chip conveyor has been cleaned.
Replace cooling lubricant
Observe the precautions for the use and maintenance of cooling lubricants in the section "Cooling lubricants".
Treatment of cooling lubricants in accordance with environmental regulations.
Add system cleaner 24 hours before cleaning the chip conveyor.
Prerequisite
- The power cut-off device has been switched off and locked with a padlock.
Required Tools/Materials
- Cooling lubricant
- Industrial vacuum cleaners
Process
- Cut off the electrical connection and unplug the delivery hose.
- Push the cooling lubricant from the chip conveyor.
- Pull the chip conveyor forward under the machine tool.
- Thoroughly clean the chip conveyor.
- Pack the chip conveyor under the machine again.
- Diluted cooling lubricant has been added through the chip conveyor.
- Check the liquid level.
- Repeat the Process if necessary.
- Cooling lubricant has been supplemented.
Check the tension of the conveyor belt
Prerequisite
- The power partition unit is off and locked with a padlock.
Process
- Raise the conveyor belt from below by pressure.
- The conveyor belt must be raised about 10 mm.
- The dimensions (x) must be equal on both sides.
- The tension of the conveyor belt has been checked.
Adjust the tension of the conveyor belt
1. Tighten the hanging plate 2. Clamp nuts 3. Lock nuts
Prerequisite
- The power partition unit is off and locked with a padlock.
- Clean the conveyor belt.
Process
- Unlock the lock nuts (3) on both sides.
The conveyor belt is not evenly clamped. Propeller shaft bending.
Slowly strain the sides.
Turn the clamping nut (2) connected with the tension hanging plate (1) evenly in the direction of the arrow.
The tension of the conveyor belt has been adjusted.
4.14.21 Flip round table
4.14.21.1 Overview of maintenance work
- Lubricate the nozzle with dilute grease.
Lubricate the nozzle with dilute grease
Lubricate the 2 lubricating nipples with dilute grease after every 250 operating hours.
4.14.22 Geometric measurement
After a tool, machining spindle, or spindle box collides with a workpiece or other device, you must check the geometry of the X-, Y- and Z-axis.
4.14.22.1 Overview of maintenance work
- Check the geometric accuracy of the X-, Y- and Z-axes.
Inspection of geometric accuracy
After geometric measurement, it must be activated again depending on the compensation position.
Prerequisite
- Location-dependent compensation has been deactivated.
- Spindle position compensation has been activated.
Required tools/Materials
- Test mandrel (300 mm)
- Micrometer
Process
- Check the radial runout of the spindle at least at two points with the test mandrel.
- Use a micrometer to check the verticality of the spindle relative to the work surface (X- and Y- axes).
- Use a micrometer to check the parallelism of the worktable with respect to the X - and Y-axes.
Geometric measurements have been completed